For this installment of Watch Affinity’s Spotlight, we have decided to take a look at an independent brand that are bringing a fresh take to the age-old art of enamelling and enamel dials. In this article we will take a look at the history of enamel dials in watchmaking, explore the current Bereve Timepieces collections and shine the spotlight on this independent manufacture from the Swiss town of Chiasso, near the beautiful Lake Como.
What is enamelling?
Let’s start by looking at enamelling, and what exactly an enamel dial is. Enamel dials are certainly not new; indeed, enameling as a decorative art has been around for many hundreds of years, with some sources citing that the first recorded use of enamel work dates to the 13 Century BC in Ancient Greece. Stripped back to its bare, enamel is simply a transparent glass material which has been coloured using metal oxides – when enough heat is applied (around 800°C), it melts and fuses with the metal base beneath it.
Throughout the history of watchmaking, various techniques of enamel work have been applied to the metal base of both dials and cases of pocket watches as a decorative feature. Today it is still used by many brands in addition to Bereve Timepieces, some in the form of high-end artisan pieces with decorative enamelling such as Vacheron Constantin and Blancpain, as well as others with a more simplistic effect on the dial such as Breguet. There are also some more accessible brands which offer enamel dials, including AnOrdain (who even offer a fumé style enamel dial) and Seiko.
In order to produce these different results, there are of course different methods and techniques which are employed. Let’s take a look at some of these in turn:
Grand feu/vitreous
The name itself refers to the process, with ‘grand feu’ translating to ‘big fire’. This is a technique used by many manufacturers, whereby the decorative enamel is built up with a multitude of layers, one atop the other. On the surface of it, this might sound easy, however completing a brilliant and perfect enamel finish is fraught with difficulty.
Multiple layers are required to be added in order to achieve the deep and rich colours required, each of which needs to go through the firing process. Every step inherently risks creating a hairline crack, bubble, or even just the slightest imperfection in the dial, which ultimately renders it unusable. This happens frequently, even dedicated companies with the finest enamellers – one such company is Donzé Cadrans, who are understood to abandon 60% or more of dials attempted.
Cloisonné
Whilst the general principle and process of enamelling is applicable here too, this technique allows for a more detailed and intricate pattern to be created. The enameller applies a tiny gold wire, finer than a hair, to the dial to create the pattern – the wire essentially serves to form a barrier as it is raised above the base of the dial, creating segments that can be filled in colour by colour.
The technique still requires these colours to be built up using multiple layers, but the enameller must also factor in that different colours of enamel will fuse to their base at different temperatures, in turn adding to the complexity.
Champlevé
If cloisonné enamelling sees the creation of segments by building up a barrier in the form of a wire, champlevé enamelling can be considered the counterpart – the dial base is engraved with the pattern instead of placing a wire, with the hollows created by the engraver then filled by the enameller and used to create and build the pattern in much the same way as cloisonné.
Plique-à-jour
This technique is similar in execution to that of cloisonné, however with plique- à -jour there is no base/backing in the final product. This means that the final product is a piece of translucent enamel work which allows the light to shine straight through, achieving the same overall effect as with a stained-glass window.
Miniature paintings
Finally, this technique (as the name suggests) requires the artisan to create the desired image on a base which has already been enamelled on both sides. The colours are built up, layer by layer, with the lighter colours applied at the end. Just as with the others, this technique is prone to any attempt at firing causing irreversible damage to the overall enamel work – I cannot begin to imagine how heart-breaking this must be after spending an inordinate amount of time working on a beautiful piece of craftsmanship only to see a hairline crack on the final firing.
Hopefully from this you will get some sense of the difficulty involved in crafting timepieces with enamel dials, and an understanding as to why they often have a high price associated with them. With this context, it is time to turn our attentions to the topic of this Spotlight feature – Bereve, an independent brand and relatively recent addition to the world of haute horology.
Bereve Timepieces – an independent manufacturer
The undoubted hallmark of a Bereve timepiece is the unique enamel dials, which in 2019 earned a pre-selection by the Grand Prix d’Horlogerie de Genève (GPHG) for the Artistic Crafts award alongside the likes of Hermès, Jacob & Co and Chopard, eventually won by Voutilainen. All dials crafted by Bereve timepieces all start from a base dial that is either 24ct gold, or 999 silver, which is engraved and made by the hands of a master goldsmith. Depending on the design of the piece, the artisans will use one of the champlevé cloisonné or plique-à-jour techniques to bring the dial to life. The use of each technique depends on the results required, which of course depends on the collection that the piece would fall into.
Numbers collection dial design
The Numbers collection is the result of 18 months of research and development, and the collection which earned Bereve Timepieces a pre-selection in the 2019 GPHG awards. The decoration on the dial consists of a mosaic which depicts the numbers one would expect to find on a dial, however they are blended and interweaved into an extraordinarily complex design by Ugo Nespolo, the Italian painter and sculptor. The design consists of 132 individual ‘blocks’, which are created on the gold base of a dial using the champlevé technique, and then 20 different colours of enamel are added to complete the overall effect. Each dial takes around 150 hours of work to produce and would entail between 15 to 18 instances of firing the enamel.
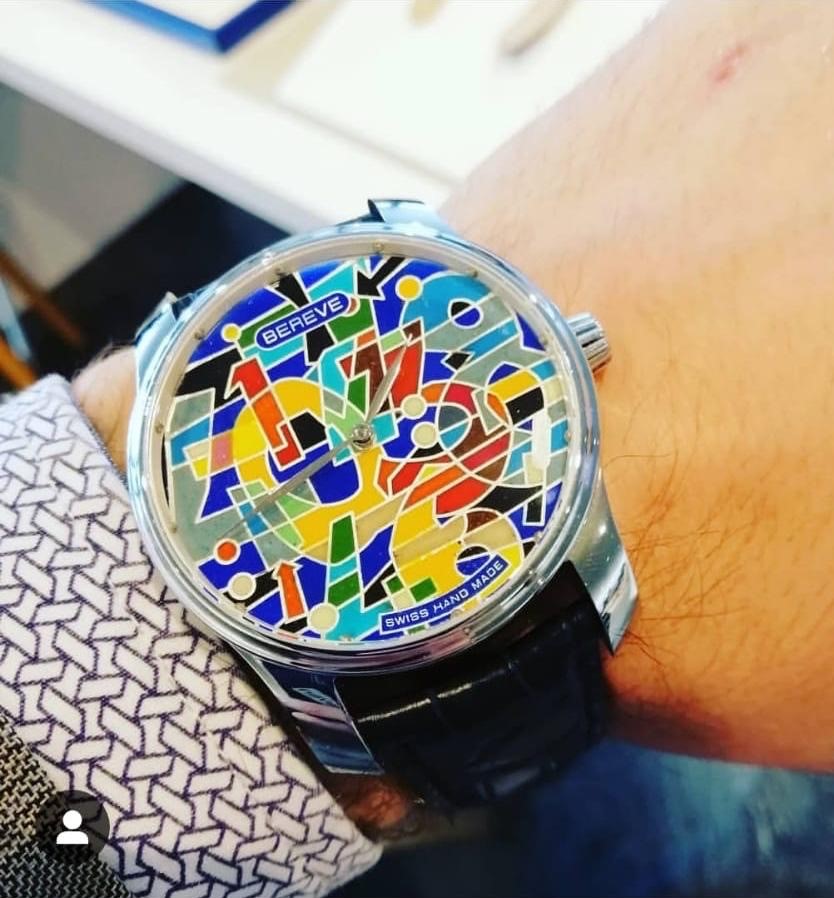
Bereve Timepieces – Numbers collection, picture: A Timepiece of Heaven
Bereve Timepieces Polygonal Prime collection
Similar in execution and design to the Numbers collection, the Polygonal Prime collection uses the same process and technique to produce a dial with a less busy design, consisting of 4 overlapping polygons and 13 individual ‘blocks’, 4 of which are part of a deep black “background” to the design. This again uses the champlevé technique, although for this simpler pattern only 10 different colours of enamel are required.
Bereve Timepieces Emperor collection
The Emperor collection stands out from the other Bereve Timepieces collections as the only one to be created using the grand feu technique, with each dial in the collection comprising only one colour. It is however also the only collection to offer a choice in variety of colours available, where you’re able to choose from white, ivory, blue, black grey or red, with a contemporary design of Roman numeral indices adorning the enamel work. For the white and ivory colour dials, there are also options for the colour of indices, too.
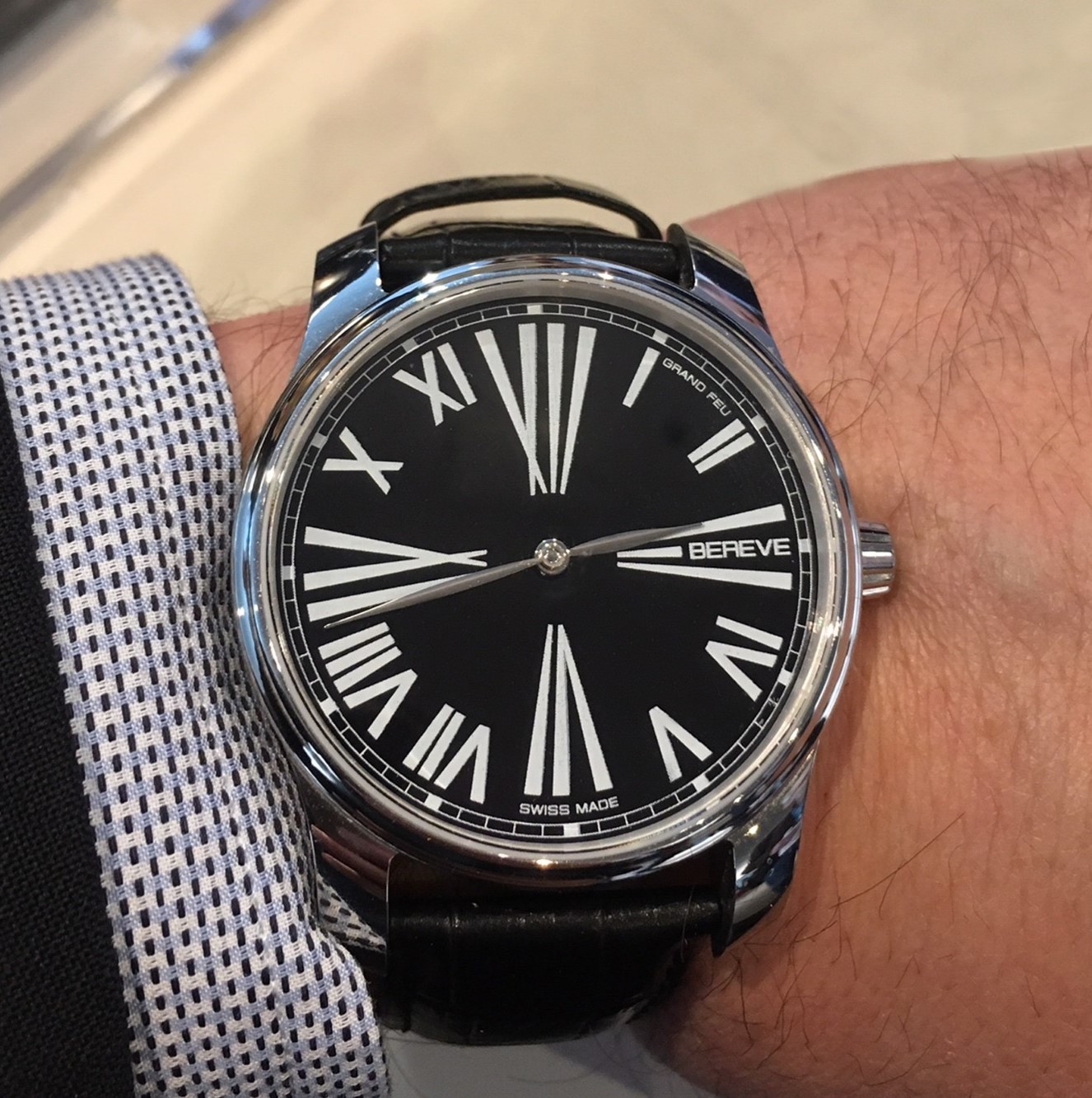
Bereve Timepieces – Emperor collection, picture: A Timepiece of Heaven
Of course, a luxury timepiece is not all just about the dial – there are many other facets to consider. The case design is the same across each of the three collections, designed in-house and manufactured in Switzerland. Each case is 42mm in size and offer 50m water resistance, and they are available in gold, stainless steel, or DLC coated stainless steel. The steel used is advanced 316LM steel, which provides a better finish and is more resistant to everyday wear and tear than traditional 316L steel. The cases are adorned with anti-reflective sapphire crystal to ensure that the showpiece enamel dial can be fully appreciated.
Each timepiece is automatic, with movements that are based on the Vaucher Manufacture Fleurier VM-3002 calibre with hour and minute functions (Vaucher is a Swiss manufacture which interestingly separated from Parmigiani in 2003 to form its own entity, and today produces movements for the likes of Parmigiani and Hermès). This movement offers an impressive power reserve of over 50 hours. The straps are the only thing not produced in Switzerland – each comes with an Italian made, hand-stitched alligator leather strap, produced in compliance with the Convention on International Trade of Endangered Species of Wild (CITES).
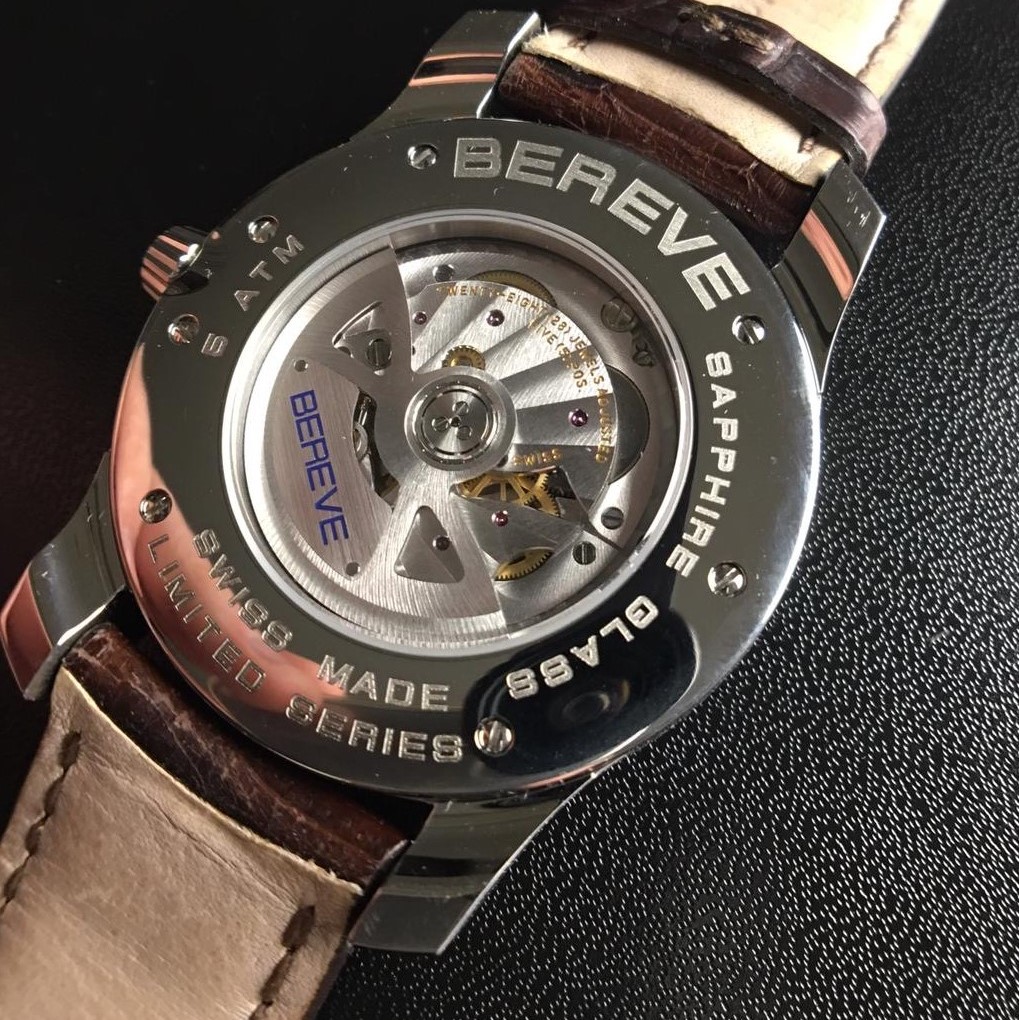
Bereve Timepieces caseback, picture: A Timepiece of Heaven
In summary
In the world of horology, I always find it particularly interesting to keep an eye on what some of the smaller independents are doing – without a multi-million-pound marketing budget, they often have to rely on the quality of what they produce speaking for them. The thing that I liked with Bereve Timepieces is that in an era when a lot of mainstream manufacturers are turning to the vintage aesthetic to inspire new models, they have instead taken an age old technique for inspiration, and used it to create something that both champions the artisan skill of enamelling and creates a bold and contemporary style, which I think this is both affirmed and recognised in the industry through their 2019 GPH pre-selection.
I am certainly excited to see where they take their creativity next and will be watching!
If you have any questions, or want to share your thoughts please get in touch via our Contact page, or via our Instagram.
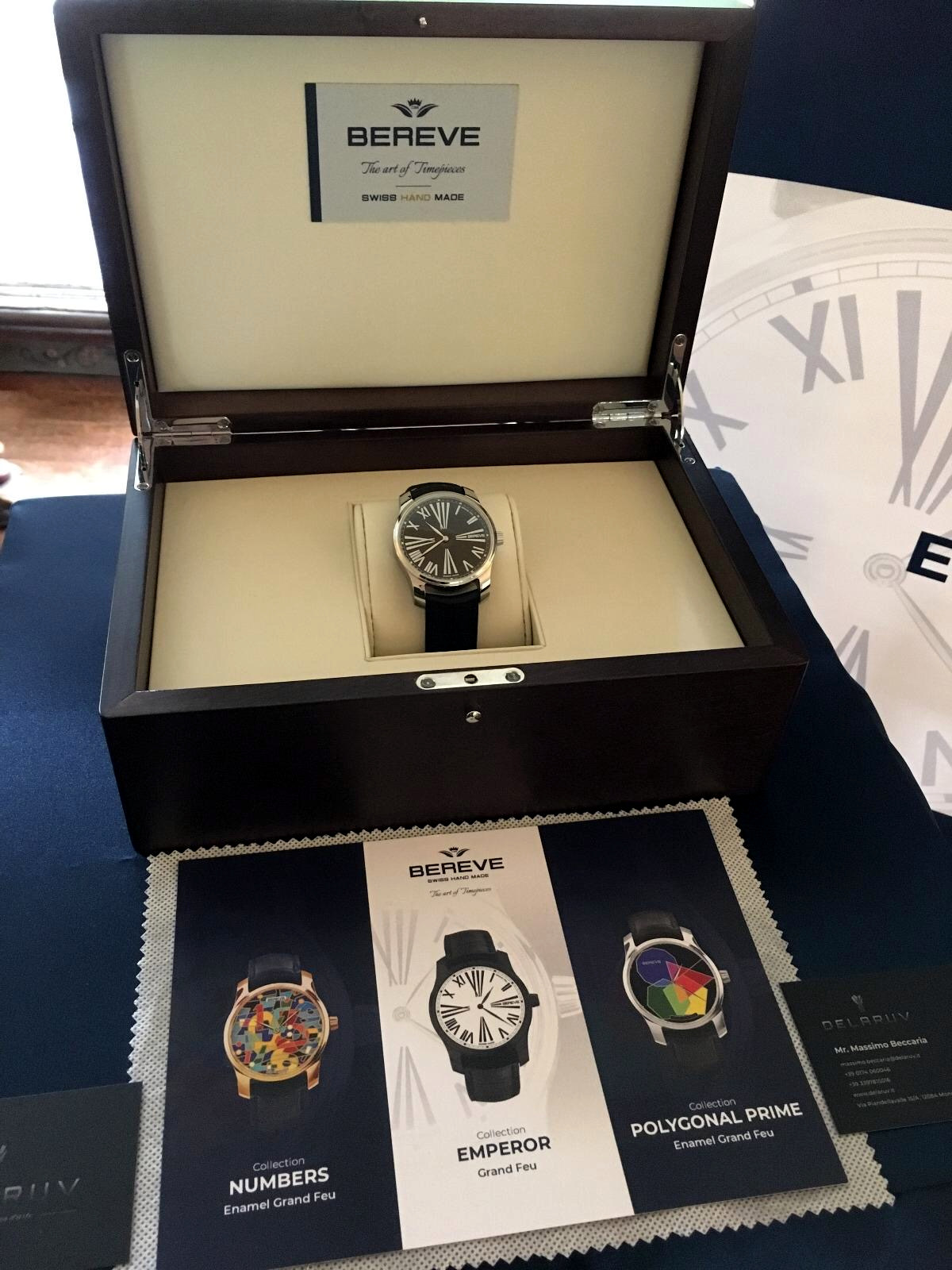
Bereve Timepieces presentation box, picture: A Timepiece of Heaven
For more information, please visit Bereve Timepieces
(With thanks to UK retailer ‘A Timepiece of Heaven’ for the use of photographs)
You might also be interested in:
- Exploring different watch enamelling techniques
- Spotlight: Grand Seiko
- Watch Finishing Techniques
- Watch Stationery and Gift Ideas
- Watch Books, Watch Boxes and more at the Watch Affinity Shop on Amazon (commissions earned)
As an Amazon Associate, I earn from qualifying purchases – thank you for your support
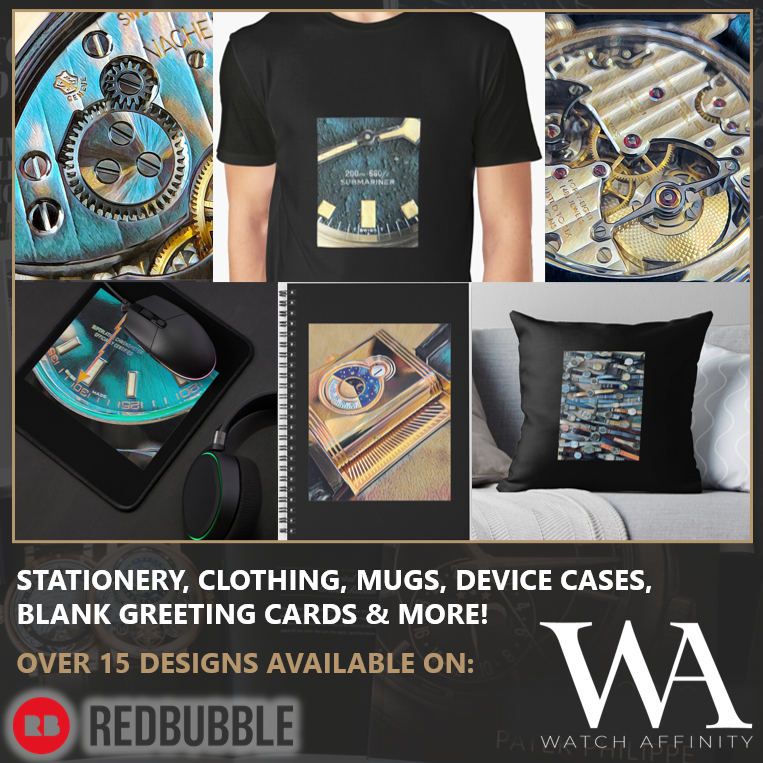
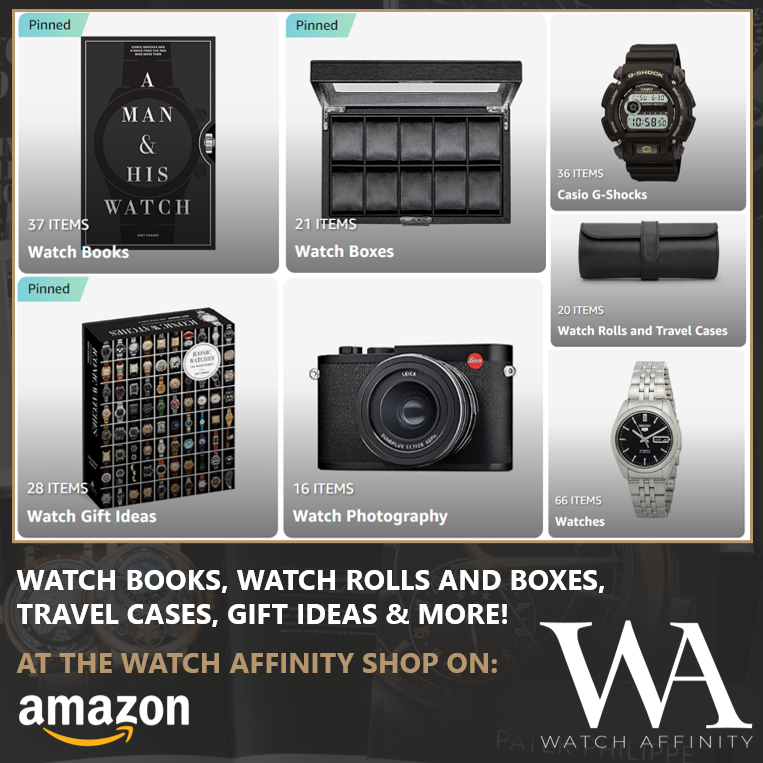