In this article, we are going to explore that art of enamelling, to help get a fuller appreciation of what exactly an enamel dial is and the work and skill that goes into creating them. We’ll look at some of the history around enamelling, and then explore some of the watch enamelling techniques used by modern day artisans to create some of these beautiful dials.
The use of enamel work in horology is certainly not a new thing; enamelling more generally as a decorative art has been around for centuries – some sources even cite the first recorded use of enamel work as dating as far back as the 13 Century BC in Ancient Greece. So, what exactly is enamel? Simply put, enamel is made from a transparent glass material which is coloured using metal oxides. When enough heat is applied (around 800°C), it melts and fuses with the base beneath it. This base can be anything from metal to glass, or ceramic to stone – in short, anything capable of withstanding the intense heat requires to melt the enamel itself.
Throughout the history of watchmaking, enamel work has been applied to a metallic base used for both dials as well as the cases of early pocket watches as a decorative feature. There are some incredible examples of early enamel work in the Patek Philippe museum in Geneva, or even the Science Museum in London.
Despite being an age-old art form, enamel today it is still used by many brands (perhaps unsurprising in a field that has itself existed for centuries!), both in the form of high-end artisan pieces with decorative enamelling such as Vacheron Constantin, Bovet, Blancpain and Bereve, as well as others with a grand feu dial such as Breguet. However, these different watch enamelling techniques are not exclusive to the haute horology manufacturers, with brands including Seiko and AnOrdain (who even offer a fumé style enamel dial which darkens toward the edge) making beautiful timepieces that equally showcase the art form.
Watch Enamelling Techniques
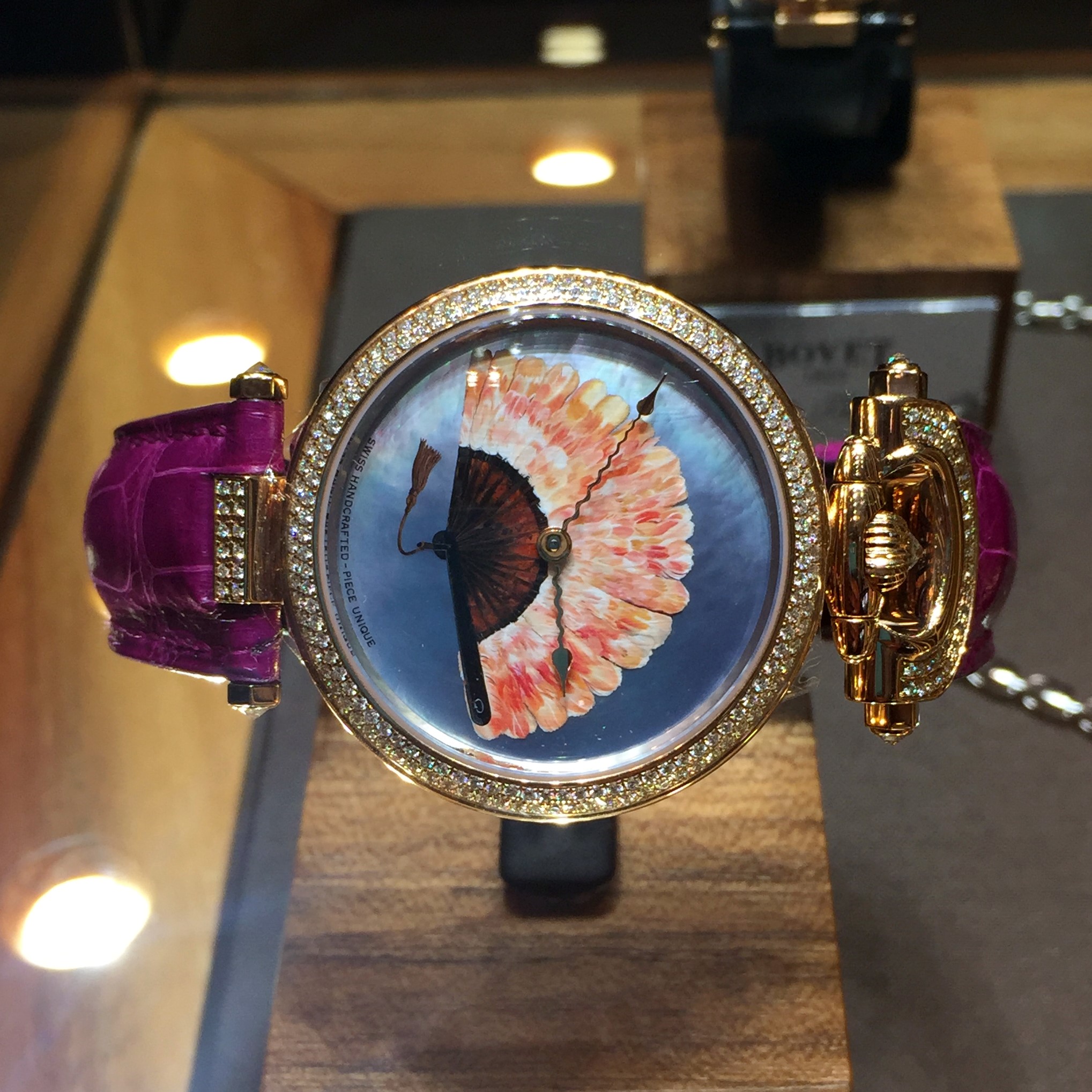
Bovet enamel dial piece unique
To achieve different effects with enamel work, there are of course different watch enamelling techniques which are employed. Let’s take a look at some of these in turn:
Grand feu or vitreous enamelling
These terms refer to the process and effect respectively, with ‘grand feu’ translating to ‘big fire’ and ‘vitreous’ coming from the Latin word ‘vitreum’ which means ‘glass’. A grand feu or vitreous enamel dial is perhaps the most common type of enamel dial found today, however despite this the technique itself is by no means the easy. The overall effect of a grand feu or vitreous dial is a beautifully rich, deep colour which covers the entire dial. This is achieved by building up many layers of the enamel, one atop the other. Each individual layer subsequently needs to be fired to allow it to fuse with the base and layers beneath it fully, which in itself is fraught with risk.
Each time a new layer is added, and the enamel dial is fired, this act risks creating a hairline crack, a bubble, or any other slight imperfection in the dial, which ultimately renders it unusable. This happens frequently, even at companies dedicated to this art form with the finest enamellers in their employ, with numbers as high as 60 or even 80% of enamel dials having to be abandoned owing to imperfections.
When holding a timepiece with a grand feu enamel dial, it is quite thought-provoking to just keep in mind how many dials had to be attempted and failed for this single, perfect dial to be created.
(An interesting side note: did you know that in 1795, Abraham-Louis Breguet came up with a ‘secret signature’ as a countermeasure to fraud? These tiny signatures are hidden in the dial and are only visible when the light catches it just at the right angle. These secret signatures are even included in Breguet enamel dials today – imagine, with all the difficulty mentioned above, then adding a signature within the enamel!)
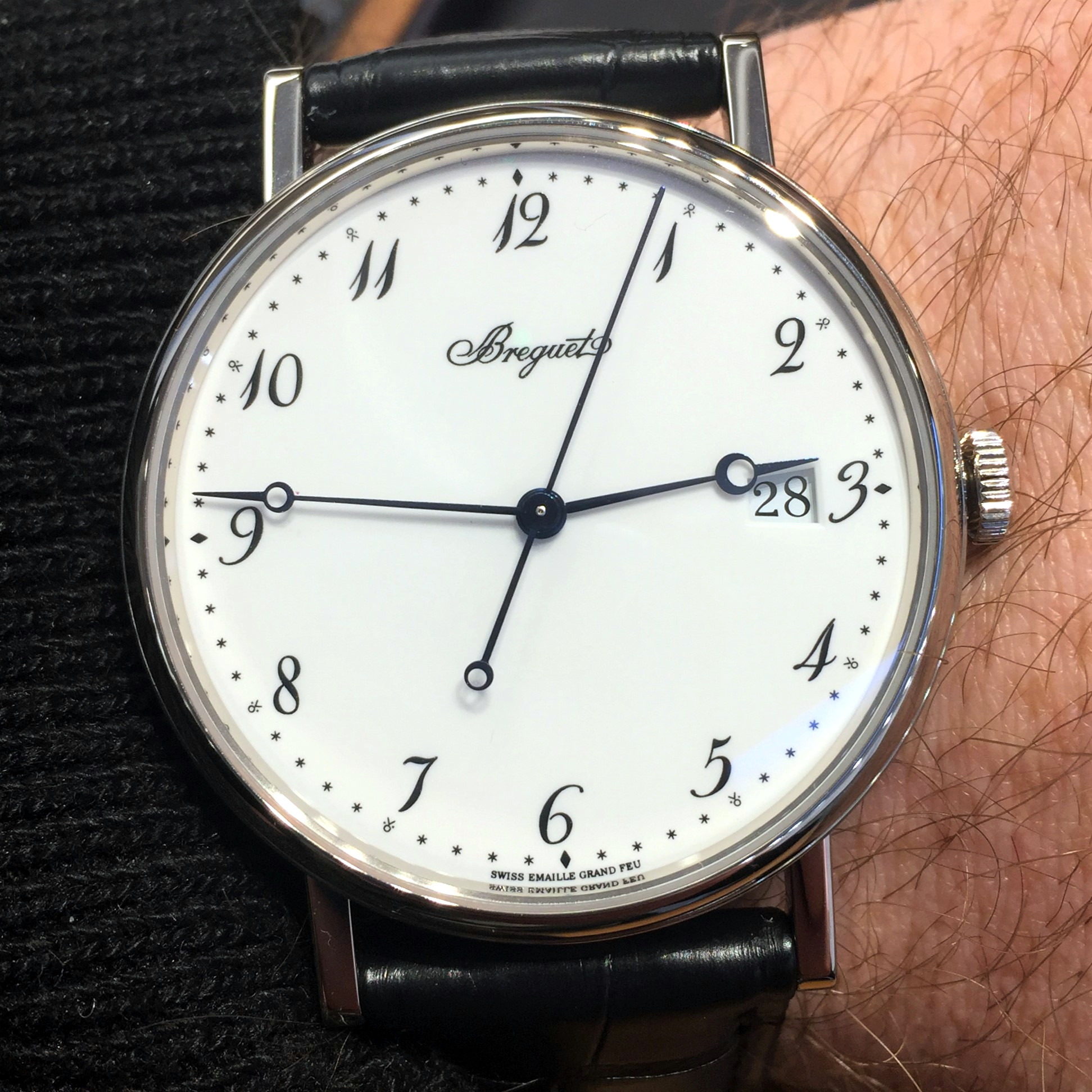
Breguet Classique with grand feu enamel dial
Cloisonné enamelling
This is the first technique we are going to explore which starts to introduce multiple colours into the enamel work. For each of these techniques, the general principle and process of enamelling is applicable, however there are additional considerations taken for building in separate colours without them unintentionally mixing or blending.
The first of these techniques is cloisonné, based on the French word ‘cloison’ which translates to ‘partition’. This technique allows for a more detailed and intricate pattern to be created, whereby the enameller applies a tiny silver or gold wire, or even a very fine strip, to the base to create the pattern – this wire essentially serves to form a fence or barrier that is fixed to the base, thereby creating separate partitions that can subsequently be filled in colour by colour. These wires remain visible on the piece afterwards.
The technique still requires that these colours be built up with multiple layers, however the complexity of doing this is increased as the enameller must also now factor in that the different colours of enamel used will fuse to their base at different temperatures.
Champlevé enamelling
If cloisonné enamelling sees the creation of segments by building up a barrier in the form of a wire or strip, then champlevé enamelling surely will be considered the counterpart. In this technique, the base is directly engraved with the pattern, which creates individual troughs or hollows in the base itself that serve to create the partitions, and these are then filled by the enameller and used to create and build the pattern in much the same way as cloisonné.
This technique was a popular choice for covering large areas or figurative depictions, although it is not commonly used today. Bizarrely, the name champlevé comes from the French words ‘champ surélevé’ which translate to ‘raised field’, even though the enamel is in fact applied to an engraved, lower area rather than one which is raised.
Plique-à-jour
There is a further technique which is an evolution on cloisonné, known as plique-à-jour. This technique is similar in execution to that of cloisonné, whereby the enamel work is applied in partitions that are separated by a wire or strip, however with plique-à-jour there is no base or backing on the final product, meaning it is rendered translucent and light is allowed to pass straight through (achieving much the same overall effect as a stained-glass window).
The additional difficulty with plique-à-jour is removing the base, which is achieved either by rubbing it away or dissolving it with an acid. This technique, as you might expect, has an incredibly high failure rate.
Miniature paintings on enamel dial
Finally, this technique (as the name suggests) requires the artisan to create the desired image on a base which has already been enamelled on both sides. The colours are built up layer by layer, with no separate partitions, and with softer or lighter colours applied at the end. Just as with the others, this technique is prone to any attempt at firing causing irreversible damage to the overall enamel work – I cannot begin to imagine how heart-breaking this must be after spending an inordinate amount of time working on a beautiful piece of craftsmanship only to see a hairline crack on the final firing!
In my opinion, this technique creates the finest overall effect as it does not have the clear lines between each partition and requires the utmost precision with the enamel as it is applied. Once you have an appreciation for the level of absolute mastery required for this technique, and then factor in both the scale of the work in fitting on the dial of a watch as well as the unavoidable rates of failure, it is only then that you can truly start to appreciate the enamel work on the timepiece in front of you.
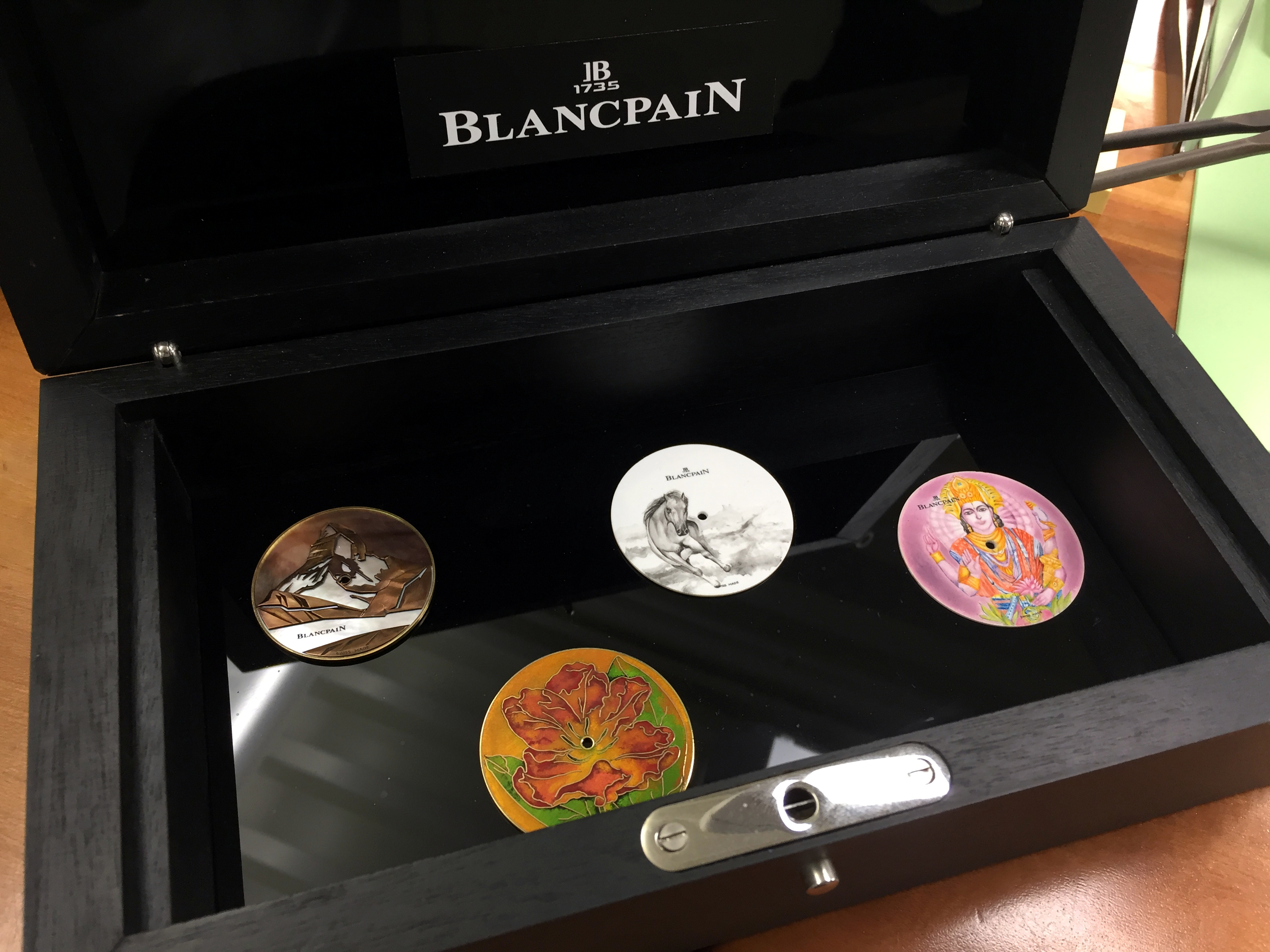
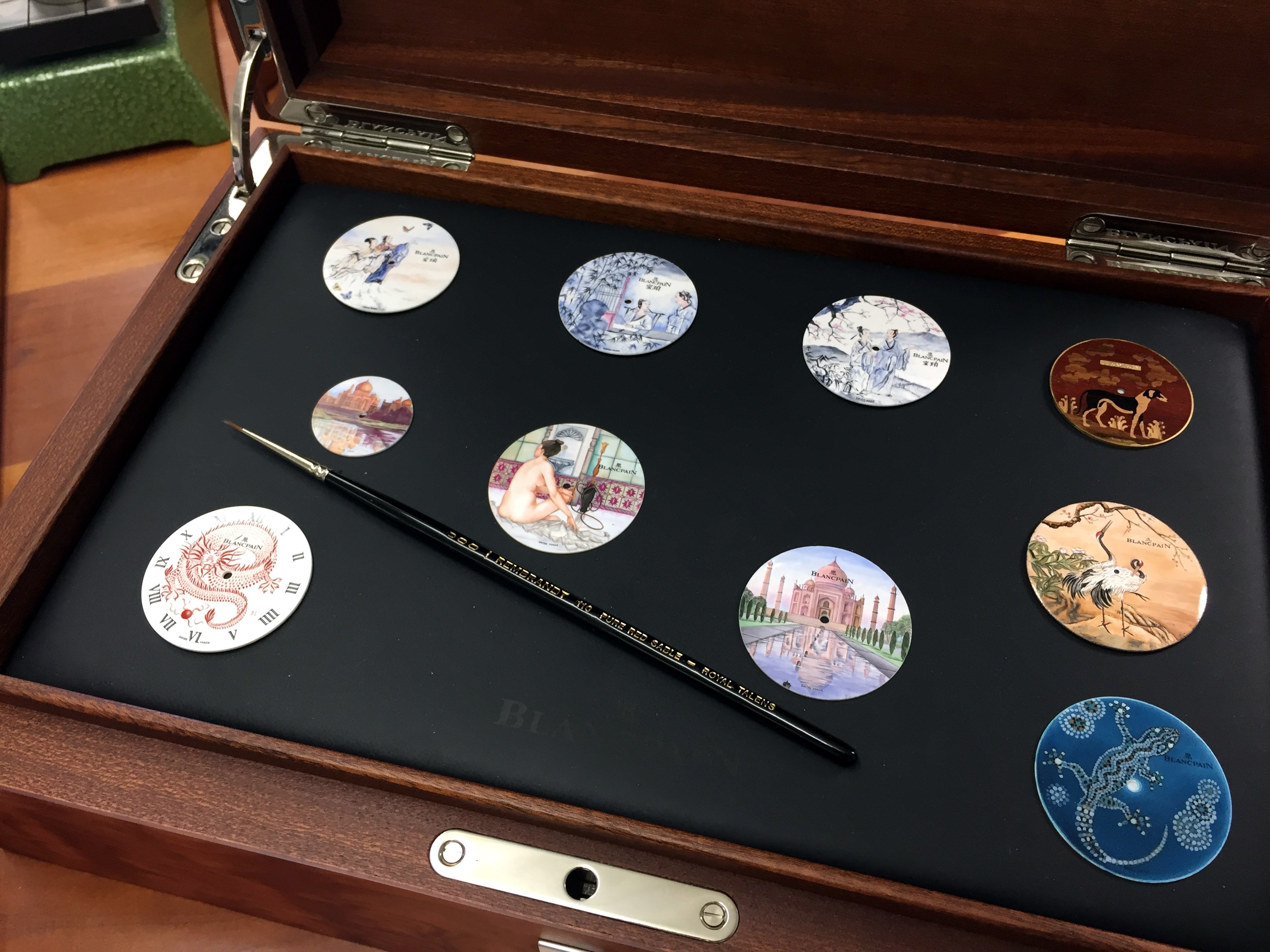
We hope this guide has helped to explain why a timepiece with an enamel dial will often come with a commanding price tag, giving you an understanding and sense of the difficulty involved in crafting enamel dials and different watch enamelling techniques.
If you have any questions, please get in touch via our Contact page, or via our Instagram.
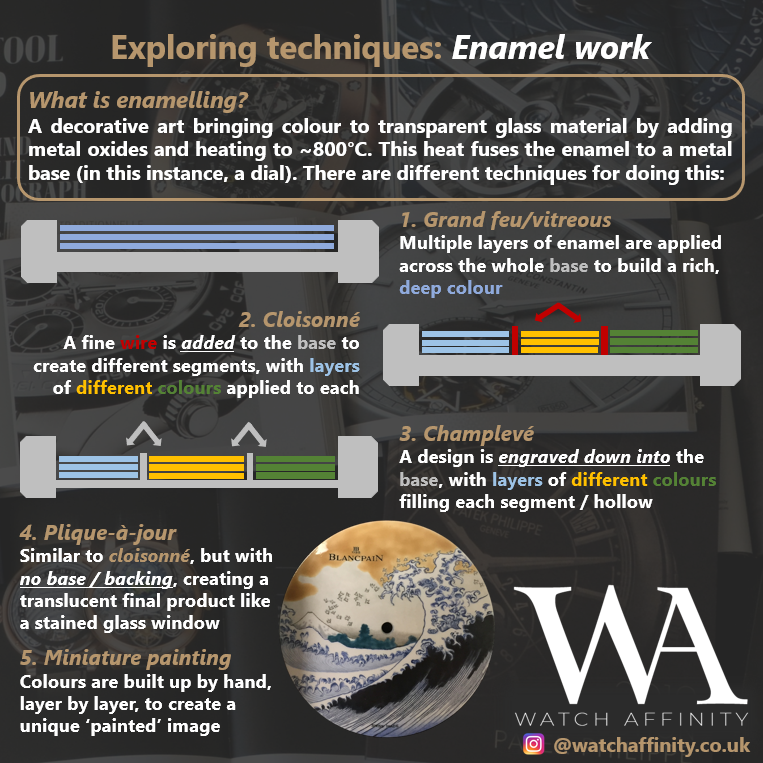
Watch Affinity guide to enamelling techqniues
You might also be interested in:
- Watch Finishing Techniques
- Spotlight: Bereve Timepieces
- A Watch Aficionado’s Guide to Geneva – Part 2
- Watch Stationery and Gift Ideas
- Watch Books, Watch Boxes and more at the Watch Affinity Shop on Amazon (commissions earned)
As an Amazon Associate, I earn from qualifying purchases – thank you for your support
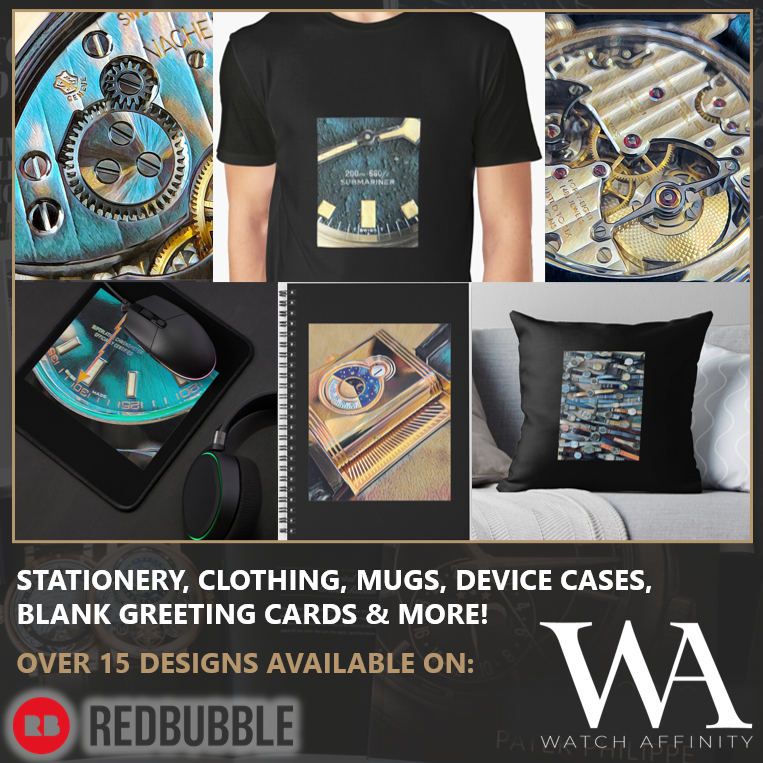
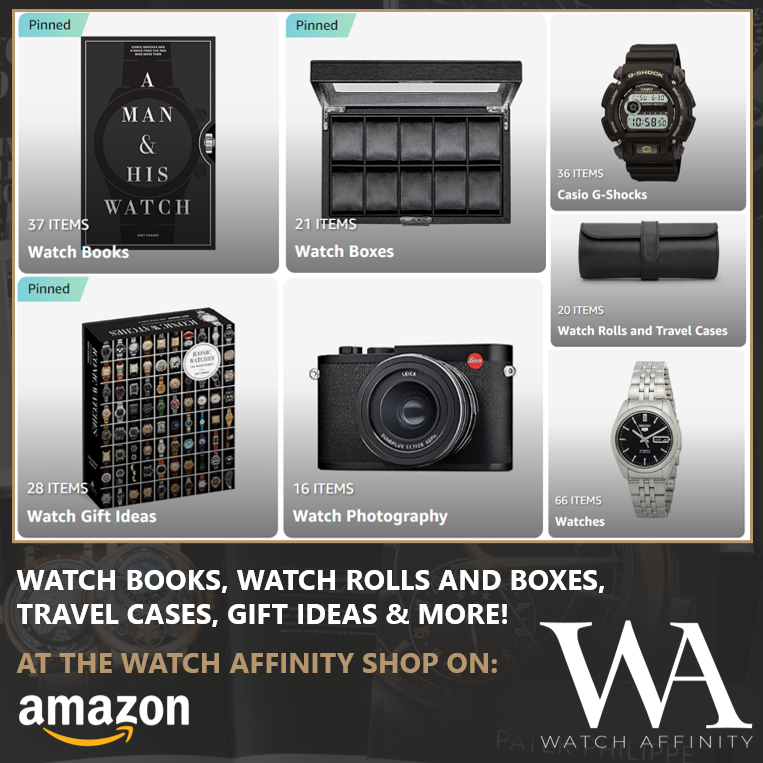