In our previous post, A Watch Aficionado’s Guide to Geneva Part 1, we set the scene as to a four-day visit to Geneva with three days exploring the world of horology plus one day of normal tourism, and recounted the first two days spent visiting a wide range of boutiques on the famous Rue du Rhône, trying on countless different timepieces, and a wonderful visit to the Patek Philippe museum.
After our day of ‘normal’ tourism visiting a chocolate factory out in the mountains, our fourth and final day was very much a case of saving the best until last: a Blancpain manufacture visit in Le Brassus!
Day 4: Blancpain Manufacture Visit
We got up early and set out to Le Brassus, which is about one hour or so away from Geneva. It was a beautiful drive, looking over Lake Geneva until we turned up into the mountains, through a few little villages and winding through some breath-taking landscape over a mountain ridge and down into a valley, where we entered the quiet towns of Le Brassus and Le Sentier, home to several high-end watchmaking manufacturers.
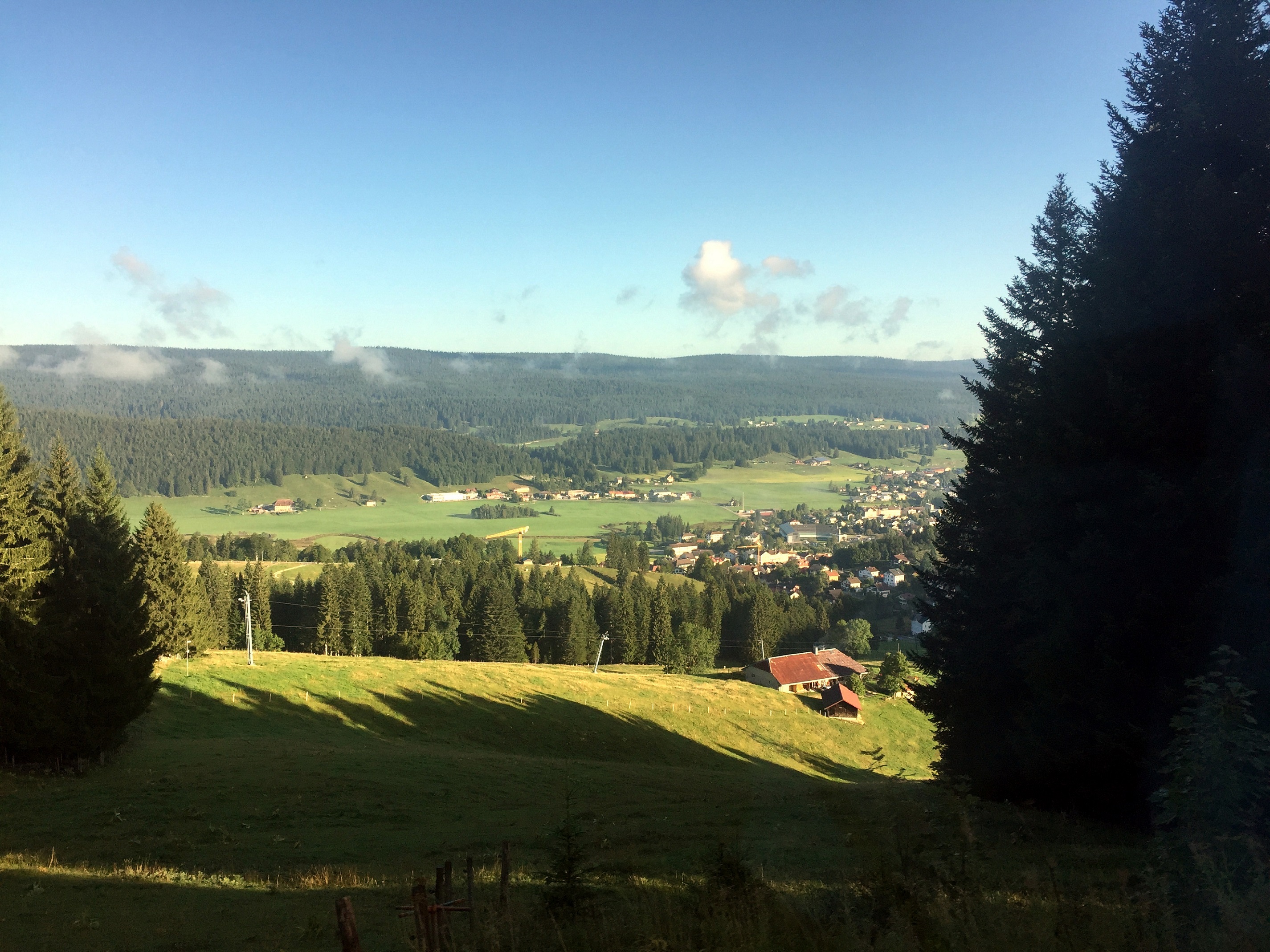
Once we arrived in Le Sentier, we met our tour guides at the main factory. The first half of our Blancpain manufacture visit would take place here, followed by a short drive back to Le Brassus to what is affectionately known as ‘The Farm’. This building was owned by Louis-Elysée Piguet where it was used as a watchmaking workshop, before becoming the location which today houses Blancpain’s departments for high-end complication watchmaking such as minute repeaters and tourbillons, Métier d’Arts and artisans who finish components by hand.
We started our visit in the main factory where Blancpain builds all their base movements. Unfortunately, it is forbidden to take photos in this building so I will only be able to describe it to you. We had the opportunity to visit the stores where roll upon roll of raw materials are kept, and to see the process by which they create each tiny component part which will ultimately find its way into a timepiece.
The progressive process by which this is completed is quite something to see and is well articulated through the pre-prepared sample pieces on hand to demonstrate the progressive nature by which these parts are created, showing the different stages that they go through; this might start with an initial one or two small holes stamped into the metal, followed by perhaps some edges and further angles or other holes.
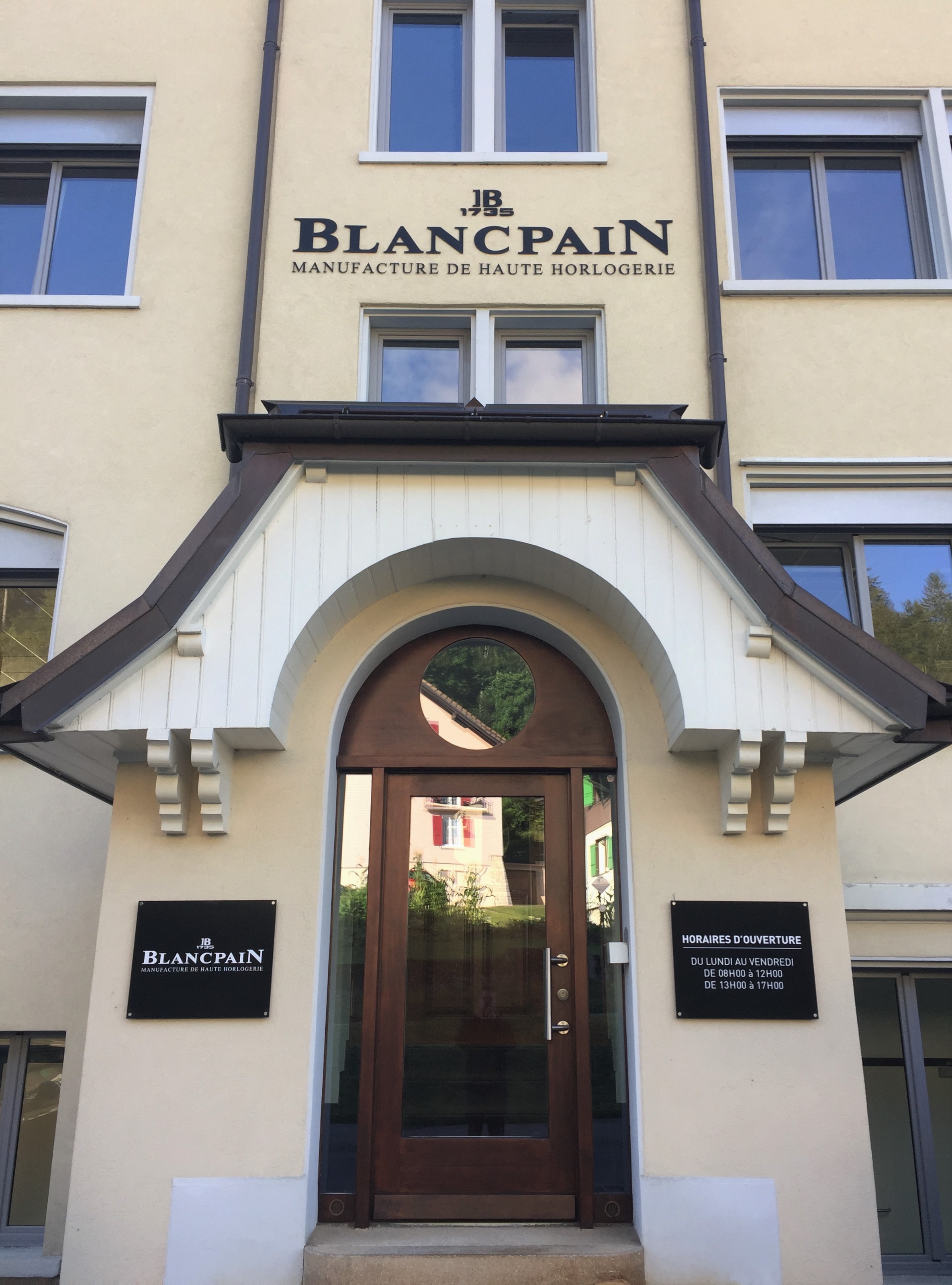
Blancpain manufacture, Le Sentier
We were shown a narrative progression through the different departments, from where the life of each tiny component begins from a roll or raw material, through to how slightly larger components such as the base plate and rotor are created. Here, we saw rotors are progressively crafted such that the outer edge remains thicker and therefore heavier with a thinner, lighter core, enabling the rotor to rotate much more responsively than it otherwise would if the weight was evenly distributed. With Blancpain, each rotor is made from 18ct gold, too – not one piece is wasted, and every single shaving will go back into the process to create more rotors.
Next, we moved into the workshop, which required us to put on some fabulous white coats and blue shoe-socks! We were able to see the watchmakers starting to amalgamate these tiny component parts into timepieces. We can all find photos of watchmaking workshops, of talented individuals working with the greatest of dexterity and diligence, but to be able to see this happen up close was incredible. We witnessed a variety of stations in the line with components coming together, including the insertion of a spring into a barrel, the placing of a balance wheel supported by a magnifying scope, and also the tuning of a completed movement to make sure that it is working to the exacting standards required by Blancpain.
Finally, to conclude the first half of the tour, we were presented with a box to inspect, containing several fully compiled base movements ready to be incorporated into wristwatches; a wonderful walkthrough of the early life of a timepiece!
Next, we paid a visit to ‘The Farm’, a short 5-minute drive away in Le Brassus. Tucked away in a secluded corner set back from the main road was a beautiful building, emblazoned with the Blancpain logo. This one-upon-a-time mill is today where Blancpain’s high-end watches are brought to life: tourbillons, carrousels, minute repeaters, and art pieces forged by the hands of Blancpain’s Métier d’Arts artisans.
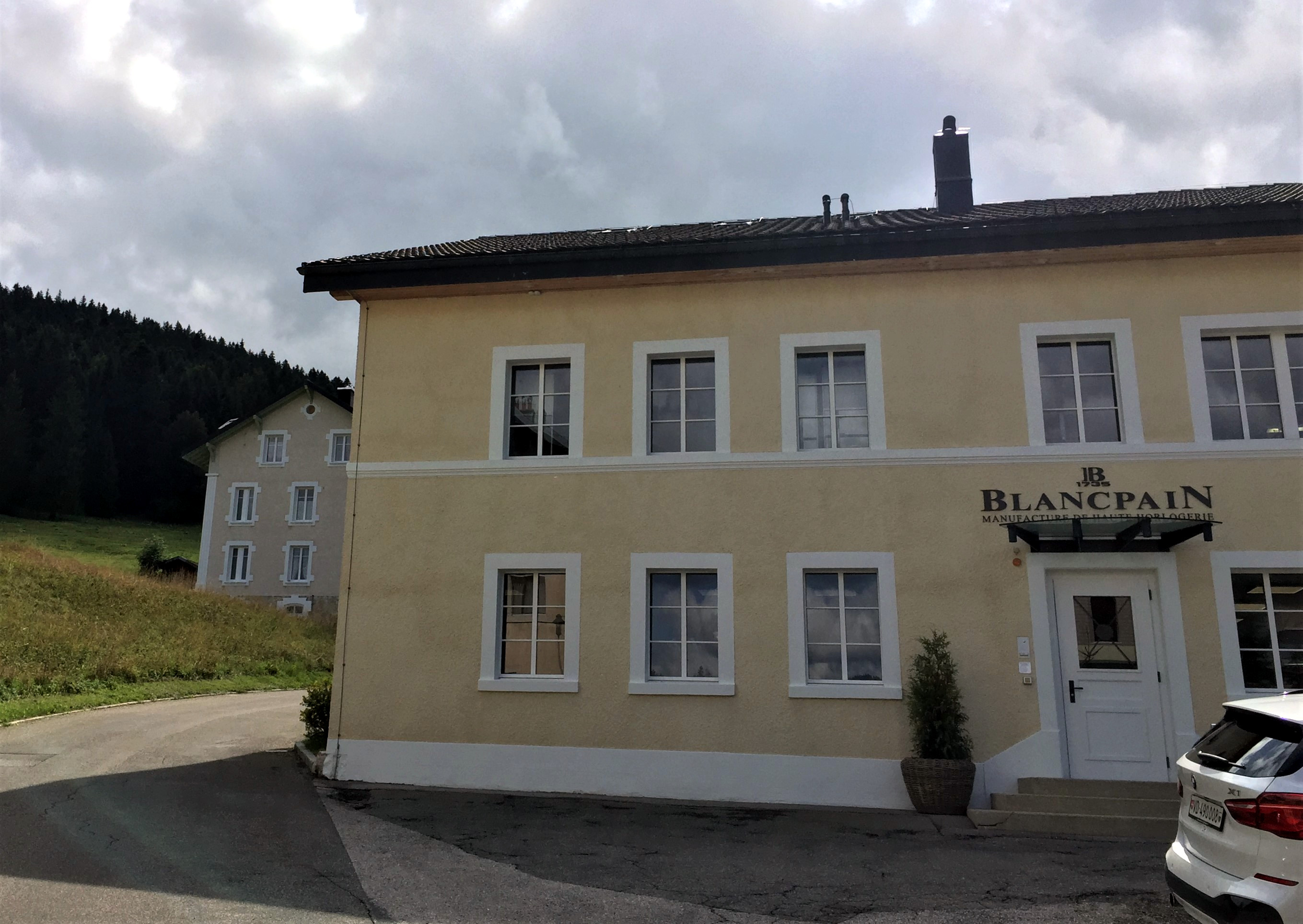
Blancpain manufacture 'The Farm' in Le Brassus
When we entered the building, there was a real sense of calm and tranquillity. A series of historic timepieces were on display in the entrance including some very early Blancpain pieces, Marilyn Monroe’s watch, and also one of the original 1735 timepieces (produced until 1991, it was at the time the most complicated automatic wristwatch and cost around £1million). This grande complication timepiece, comprising 740 tiny parts which took a single watchmaker an entire year to complete, combines the time, a full perpetual calendar with leap year indication, a moon-phase, a split second rattrapante chronograph, a minute repeater, a quarter repeater, and – of course – a tourbillon, set in a 42mm platinum case. At the top of the stairs nearby was a display cabinet featuring each tiny component part – when you see them all laid out in this way it really serves to enforce just how intricate this is.
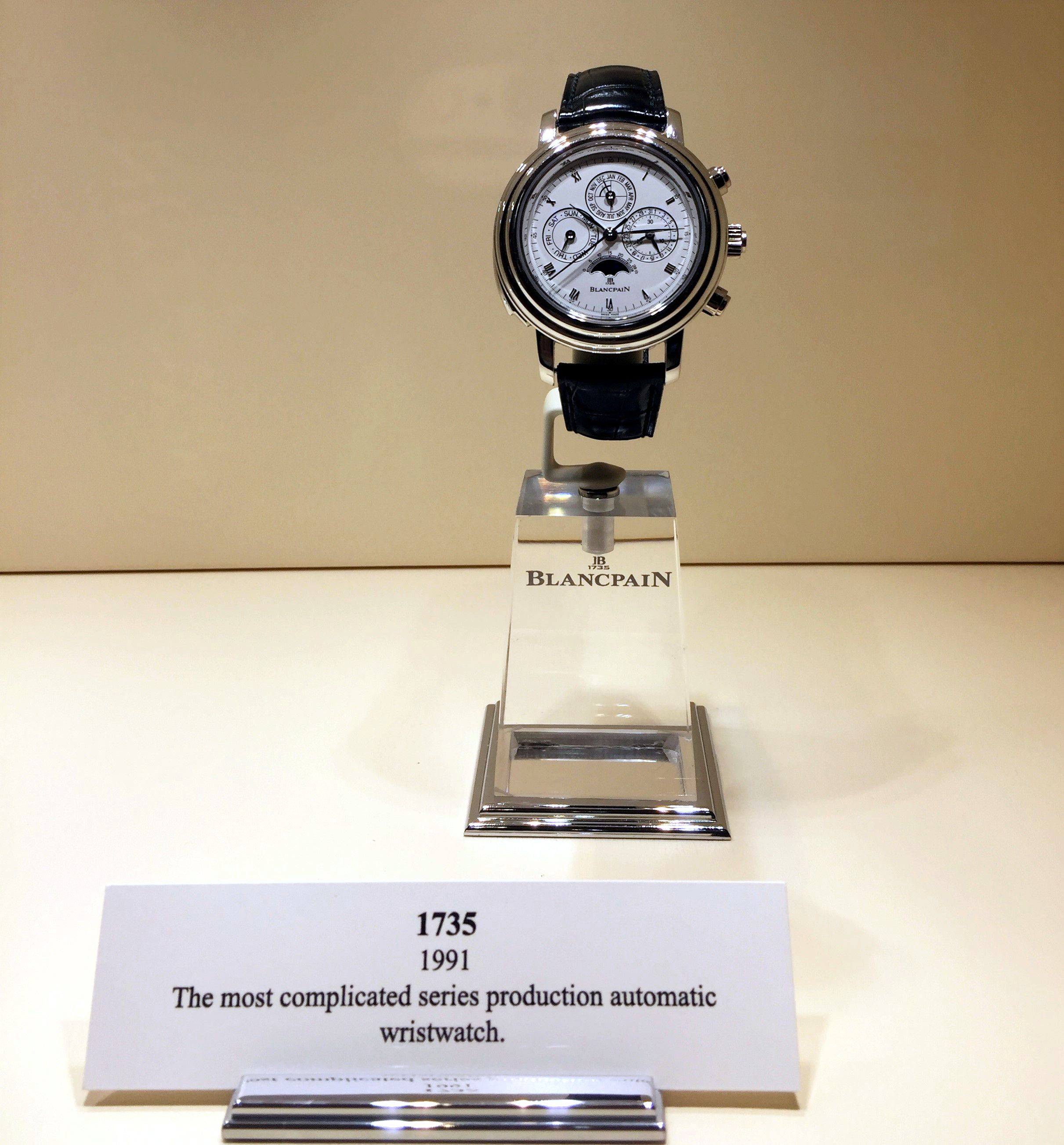
Blancpain 1735 Grande Complication
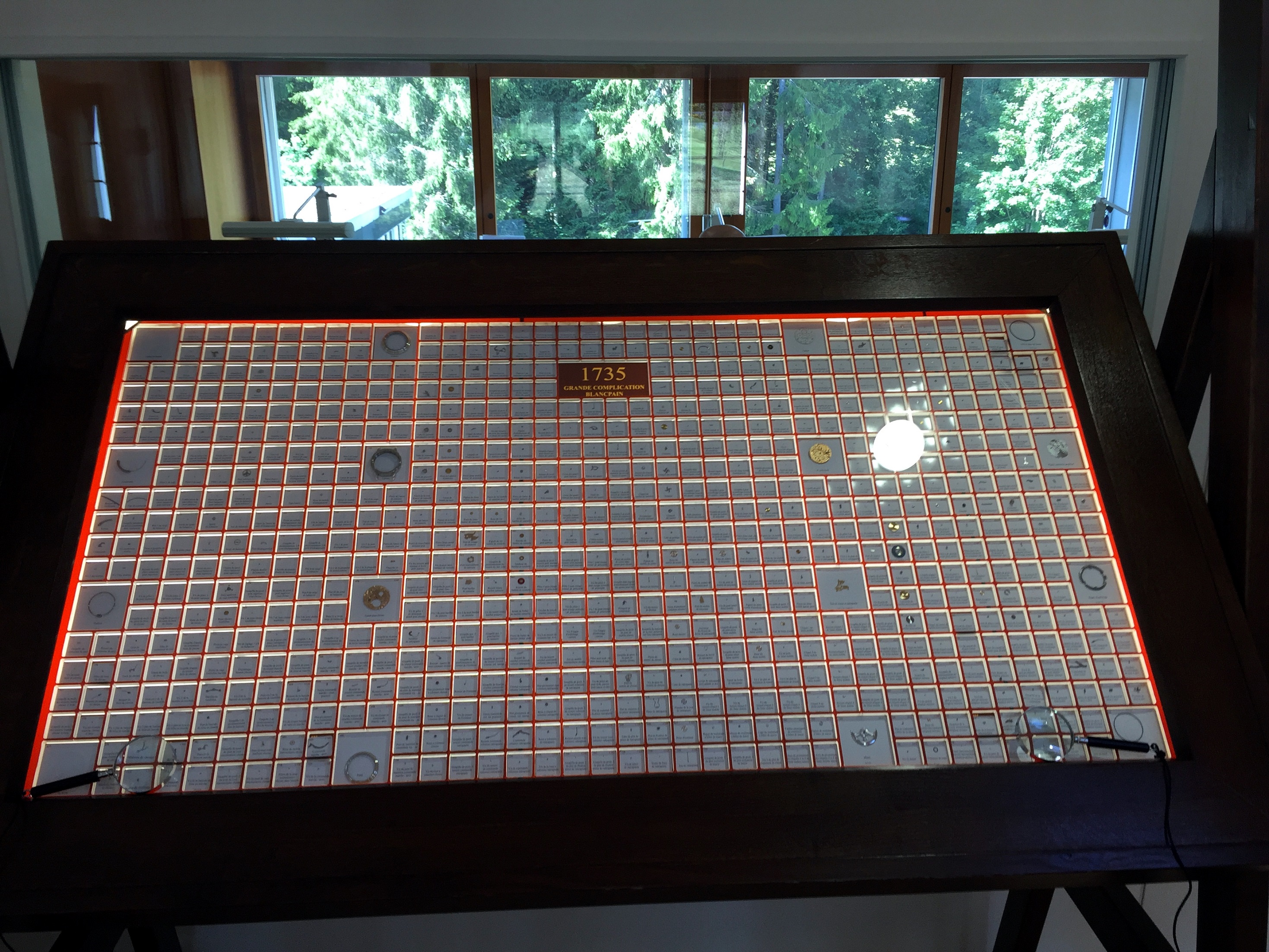
Blancpain 1735 Grande Complication components
Next we visited a few of the decorative rooms, each housing only a few artisans, where meticulous hand finishing was applied to numerous different parts. This included the rounding and polishing of edges on some components, and we also got to try our hand to perlage, the art of circular graining applied to different components, often ones with a flat face such as a plate or a bridge. The convention is to apply two circles next to each other, such that the edge of the second circle touches the centre point of the circle before it, and so on. We were shown a sample piece which took the artisan 4 hours to complete, with the additional complexity added from a variety of sizes of circles across the single component. When perlage is skilfully applied, the overall effect is quite stunning – markedly more so than our own attempt!
It’s quite sad to realise that the hours of effort spent hand finishing each of these tiny little components which end up inside the watch, would rarely or perhaps never be able to be seen or admired by their eventual owners.
We then visited the high complications rooms: the minute repeaters first, followed by the tourbillons and carrousels. Each of these rooms housed 2 watchmakers during our visit, and in each the watchmakers kindly demonstrated the complications under the magnifier and explained just how the complications worked.
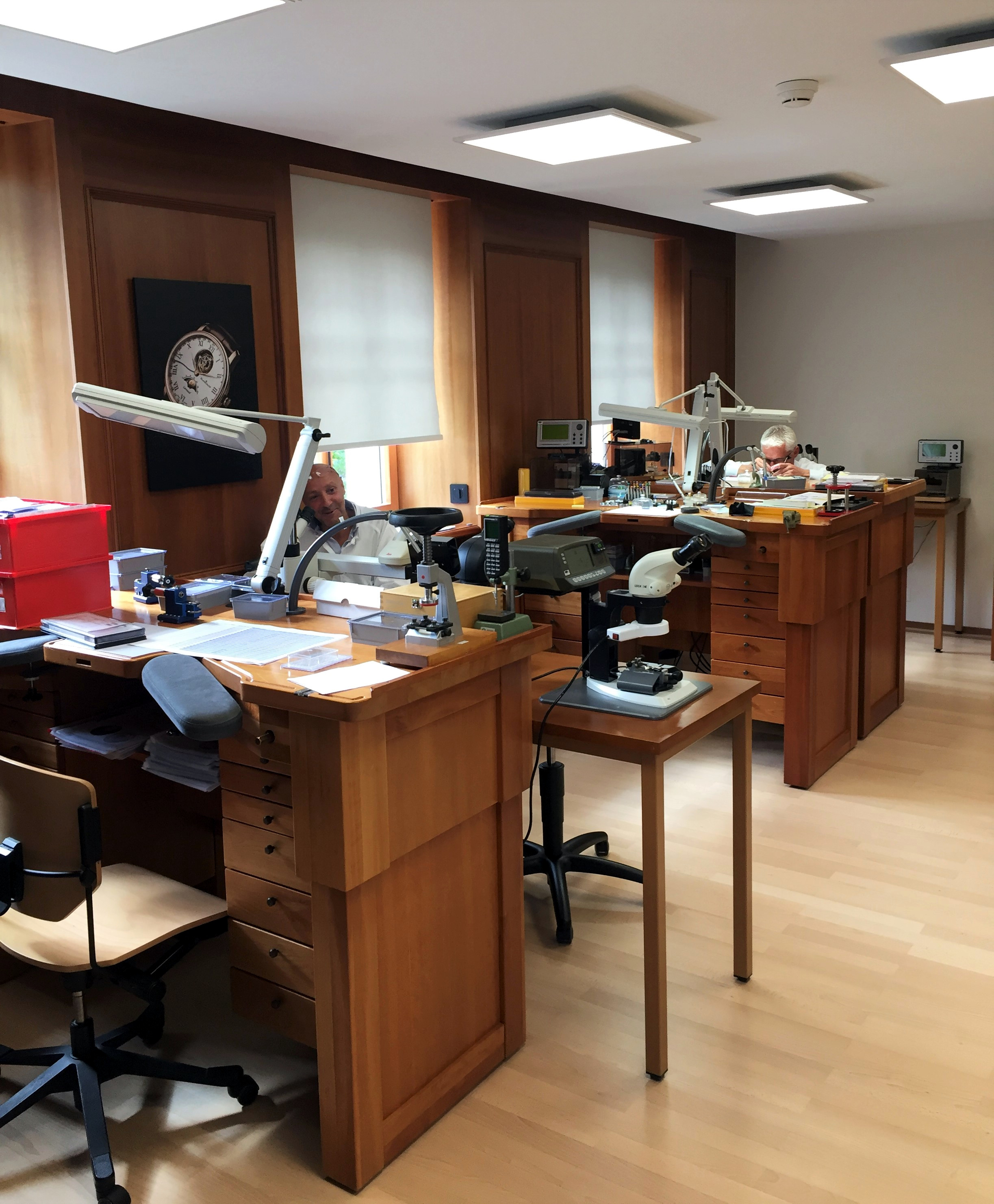
High-end complications workshop, Le Brassus
Being walked through a minute repeater complication by a master of their craft was quite humbling for me. As an engineer, my love for watches comes from the romance of hundreds of tiny parts working together in perfect synergy, and to have somebody be able to show me just how this incredible complication achieves a mechanical chiming of the time was amazing. More astounding still is that the original incarnations of this complication first appeared in a wristwatch back in 1687!
The next complication to be demonstrated was the tourbillon – one of the most difficult complications in watchmaking. With this demonstration, the watchmaker disassembled the tourbillon on his workbench such that the cage was detached and explained what the tourbillon is, and how the mechanism is fixed to the rest of the movement, before comparing the differences between a tourbillon and a carrousel. The carrousel is a more difficult complication to assemble than the tourbillon; although it was born of an idea to make something less complicated and more accurate than a tourbillon, it ended up being the exact opposite! After having watched the watchmaker show me the components under the magnifier, I happened to lift my head and glance at the bench directly, a timely reminder of just how intricate these complications are when looking down at the magnificently small components.
To put it simply, I was in absolute awe of these people, their clear dedication to their craft and complete mastery of it.
The penultimate stop on our tour was a visit to the Métier d’Arts department, something that few manufacturers today have in-house. The crafts here include engraving, enamelling, and the Japanese art forms of shakudō (an alloy of copper and gold which forms an indigo or black patina) binchōtan (engraving in a charcoal from wood fired to incredible temperatures), and damascening (laying different metals with one another). Seeing these fineries close-up was phenomenal, and the attention to detail was like nothing I’ve seen before. Everything on show crafted by the hands of these incredibly skilled individuals – one of whom even had a red and blue edge to the collar of their white coat indicating an industry award winner! The scenes depicted in the enamel dials were superlative, and we learned it is even possible for you to request Blancpain create a specific design of your own.
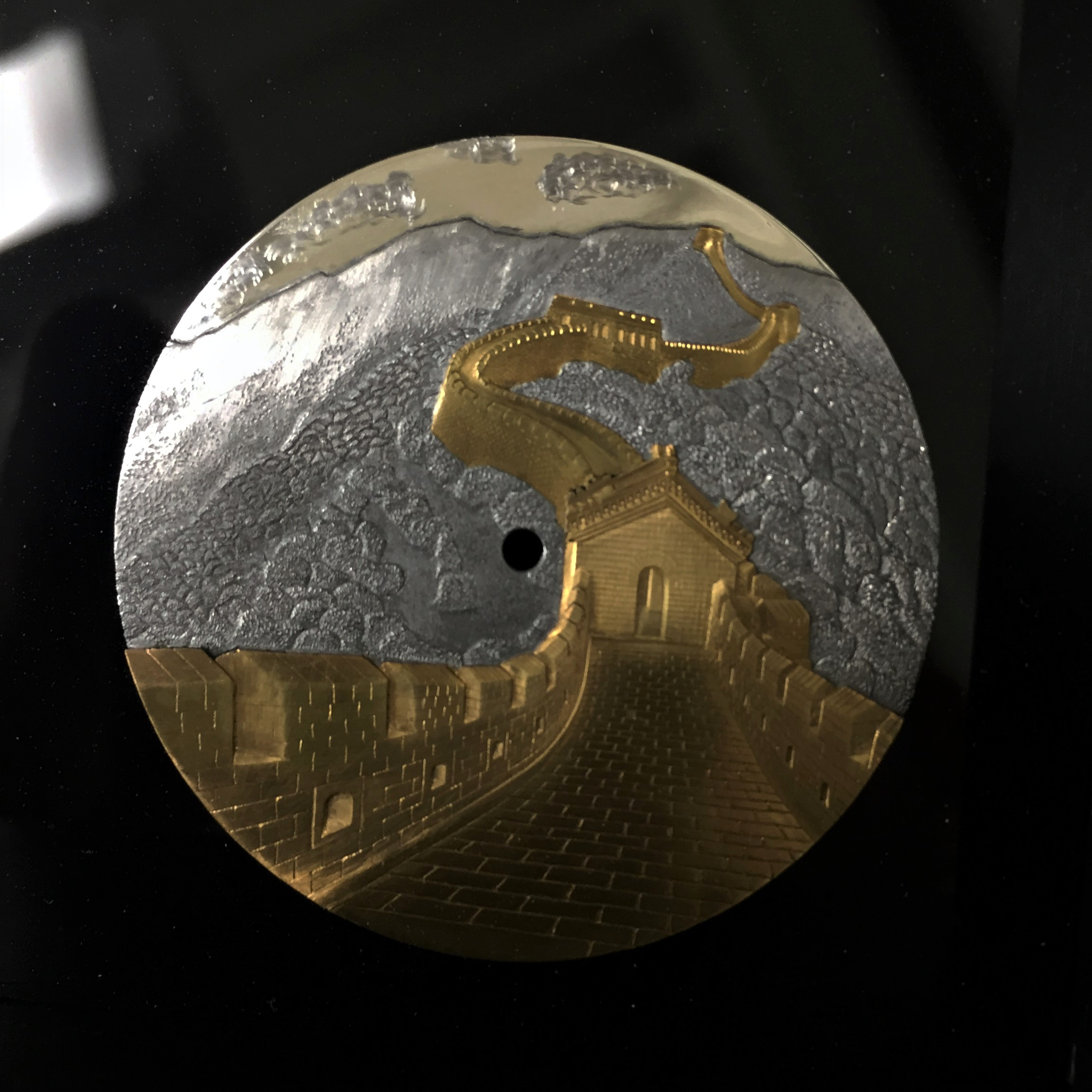
Hand engraved dial
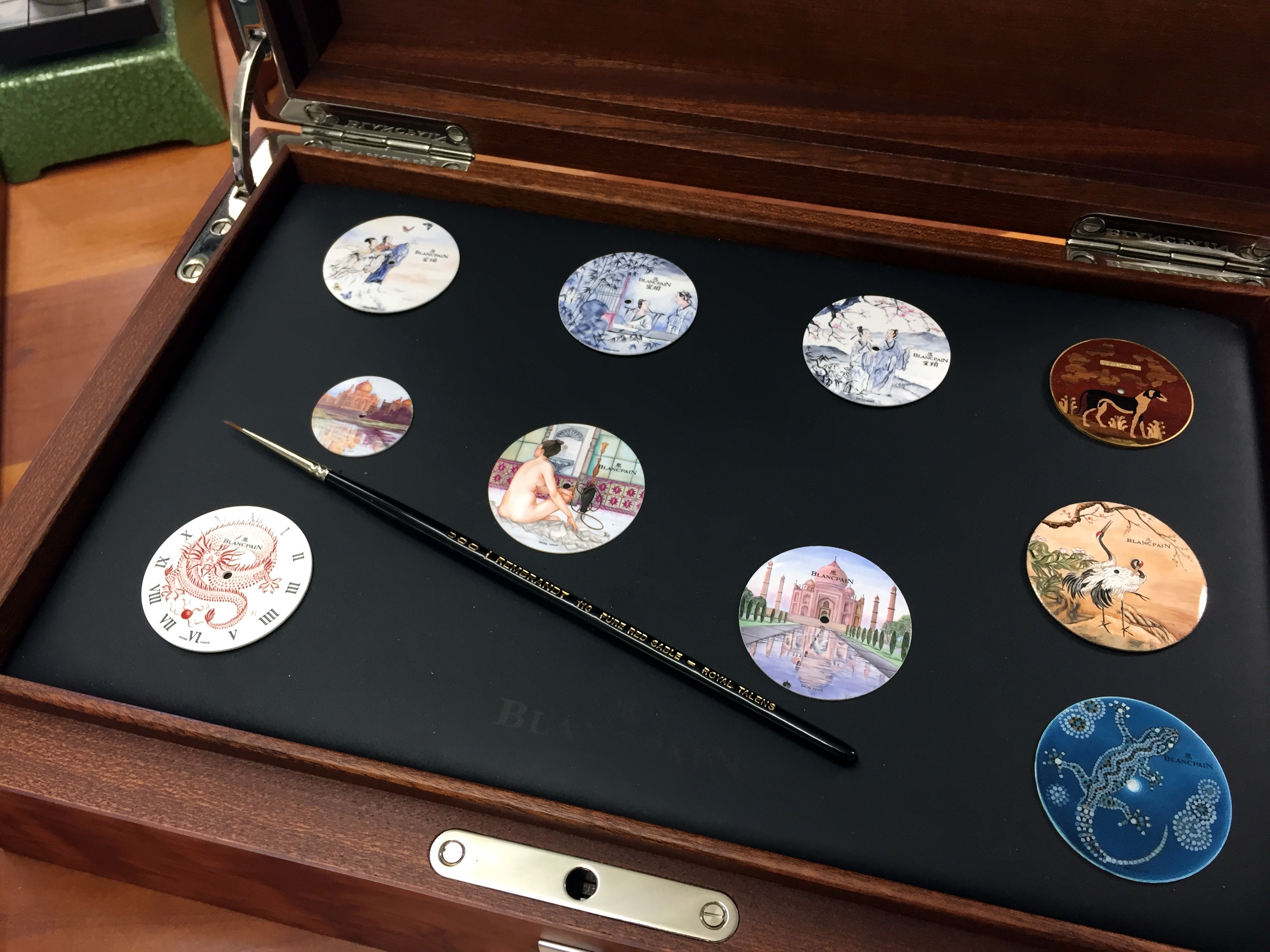
Enamelled dials
Our visit concluded with one last stop downstairs, where we were shown a variety of timepieces from various Blancpain collections, a final reminder of what ultimately comes off this very special production line.
I left our visit to Le Sentier and Le Brassus with a whole new level of appreciation as to just what goes into the creation of high-end timepieces, contemplating this on the drive back to Geneva airport to return home. This Blancpain manufacture visit and the buildings in the Swiss mountains seem a world away from the boutiques and retailers in cities around the world, and I consider myself extremely lucky to have both been able to see where each of these timepieces began and to have met some of the incredibly talented individuals and artisans who all contribute to bringing these timepieces to life. Thank you, Blancpain!
All that is left is to thank my wonderful girlfriend for an incredible birthday weekend exploring the home of Swiss watchmaking – an unforgettable experience of watch tourism in Geneva and a superb Blancpain manufacture visit! (And it was obviously a good experience for her too, as she has since purchased her first Swiss watch… mission complete!)
For any questions, please get in touch via our Contact page, or via our Instagram.
You might also be interested in:
- A Watch Aficionado’s Guide to Geneva – Part 1
- Spotlight: Blancpain Villeret or Fifty Fathoms collections
- Laurent Ferrier Manufacture Visit
- Watch Stationery and Gift Ideas
- Watch Books, Watch Boxes and more at the Watch Affinity Shop on Amazon (commissions earned)
As an Amazon Associate, I earn from qualifying purchases – thank you for your support
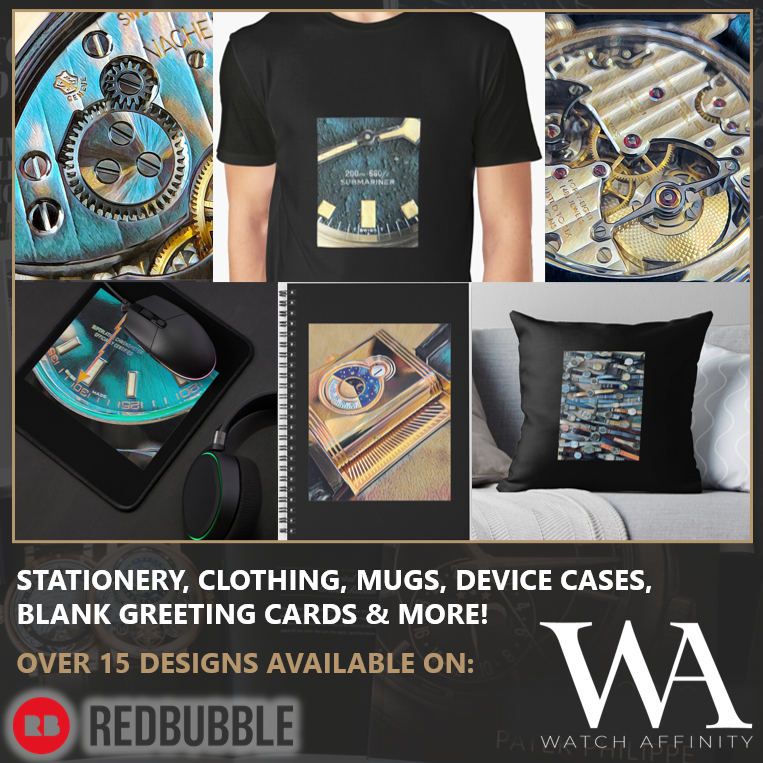
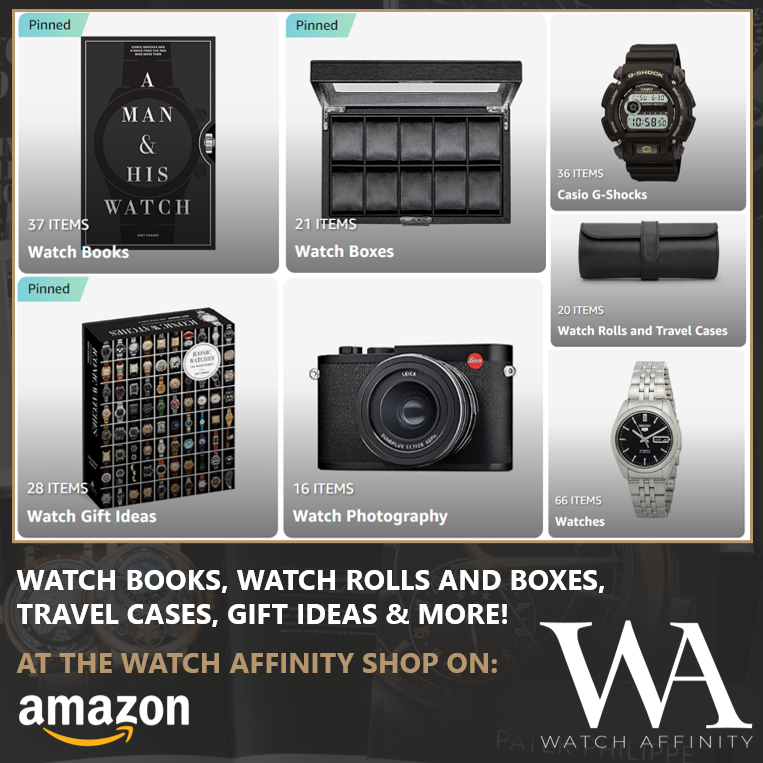