I will openly confess that until I attended the GPHG Awards in Geneva last year, I was not really aware of Bernhard Lederer or his work until he was on stage collecting the GPHG Innovation Prize for 2021.
Just as he made his way from the audience up to the stage to collect his award, the videography showcasing the Central Impulse Chronometer was playing, and to put it bluntly I was in absolute awe of what I saw.
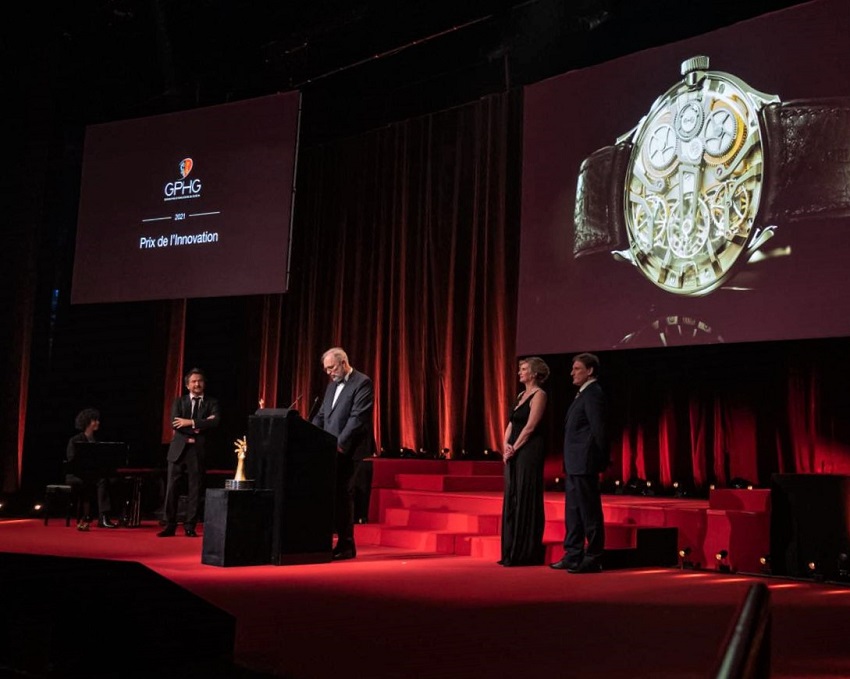
Bernhard Lederer receiving the GPHG Award for the Central Impulse Chronometer – photo, GPHG
When I returned home, I wanted to learn more about the person behind this incredible watch. Despite having been a member of the AHCI since its inception by Svend Andersen and Vincent Calabrese, quite a lot of his work is shrouded in secrecy, owing to the confidentiality agreements that come with working for Swiss watch brands.
However, with the launch of Lederer Watches, I am utterly convinced that Bernhard Lederer is a name that will be talked about more and more over the years to come – after all, there aren’t too many folks who can lay claim to their work having impressed the late great George Daniels!
A couple of weeks ago, our partners at The Limited Edition hosted a fantastic collectors’ evening in Central London with Bernhard Lederer (if you’re interested in attending such events, reach out to Pietro at TLE). This was a fantastic evening spent with great company, and it was wonderful being able to speak with Bernhard as a group, listening to his memories of George Daniels, speaking about his watches and his career, and more!
Before the event, I was fortunate to be able to interview Bernhard to ask him about his career and his plans for Lederer Watches.
In Conversation with Bernhard Lederer
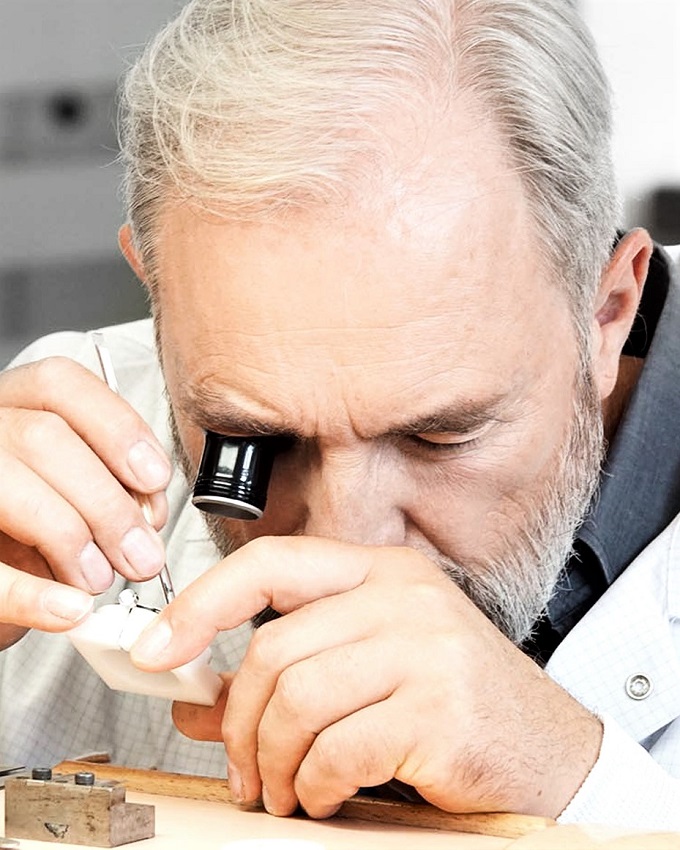
Bernhard Lederer – photo, Lederer Watches
WA: You started your watchmaking journey with a three-year watchmaking apprenticeship at the Wuppertal Watch Museum, and then started working for private clients, auction houses and the like. So, to start with, can you tell me about those early years of your career?
BL: It was tough. First of all, I had to convince my parents that I wanted to stop school and they had been very unhappy about my idea to become a watchmaker. I understand why, because everybody who was a watchmaker at that time was a battery changer because it was the time of the quartz watches! My dad proposed to teach me which way to put the battery. That was the situation I faced, but I convinced my parents. After having learned watchmaking I sent out more than 100 letters to watch shops, museums, everywhere in order to find an employment. I only got three answers, and those three answers were “sorry but we don’t need a watchmaker”!
It was a bit frustrating – you convince your parents to let you go, and three years later, you realise that maybe they had been right! I had to do something, so I came home and in my parents’ town in Stuttgart, I went to all the antique dealers and auction houses in the surrounding area to find work.
I started travelling to buy watches – London and the south coast of England were where I bought all these broken watches. I went home and started to repair them, to sell them at flea markets and auction houses. That worked quite well, so I had the chance to go to the school to become a master watchmaker, and there I built a big clock as a masterpiece. Officially there was no need to do it, but the teacher wanted us to do it, and it was clear that if you refused that you won’t pass the exam at the end.
Anyhow, I liked it, and having learned in museums and being in love with the English style of clockmaking, I made myself a skeleton clock. I made as much of the clock symmetrical as possible. We also had to do one additional function – not just hours and minutes – there should be one function more. I made a gravity escapement for that clock, and I decided to make a moon phase.
But with a moon phase, you have an error of nearly 45 minutes from full moon to full moon, so it wasn’t really at the level of a masterpiece. I was reflecting how to make a moon phase indication more precise and had an idea of making both, a moon position indication, and a moon phase indication.
By overlapping those two indications, I could reach quite a good accuracy that will be longer than my life, with the first error visible after 800 years – I considered this to be enough, and no problem with after sales service for me! I thought that if I was already working, why not make a full perpetual calendar. But not a normal four-year perpetual calendar, but one which respects the Gregorian calendar where there is not a leap year every 100 years, like the years 1900, 2100, 2200, 2300 except where the year is divisible by 4. So, in 2000 we had a very exceptional 29th February. The years 2100, 2200 and 2300 will have no 29th February. By making that system, the calendar will work for about 3200 years.
WA: I think 3200 years is pretty good isn’t it!
BL: Yes! At the end, it was that clock which I showed when I exposed for the first time with the Académie Horlogère des Créateurs Indépendants (AHCI), and this is where I met George Daniels.
Apparently, he was quite impressed as he knew quite well how difficult it is to find the good gearings for moonphase-indication. When I asked him to give me a dedication in my copy of ‘Watchmaking’ (affiliate link), the watchmaker’s bible, he noted quite short in the way how he was, that he was impressed by my clocks and that he was looking forward to seeing my wristwatches.
That is today the reason why, for the first wristwatch I made after so many years, under my own name, I decided to work on the escapement of George Daniels, the independent double wheel escapement.
WA: What a lovely tribute to Daniels.
BL: It’s a tribute, because he encouraged me, he reinforced my decision to be a watchmaker and to stay a watchmaker. As already mentioned, it was a tough time. Today, independent watchmaking is really on high interest, but at that time nobody was interested. It was a very hard living. You had to repair and repair and repair. Nothing to do with watch-MAKING.
With George Daniels I had a very interesting contact at that time as I received a request to make a reconstruction of Harrison’s H4. As I had quite detailed drawings on the H4 I was seriously reflecting whether to take the job. I do not remember why, but I thought it would be a good idea to contact George and ask what he thought.
He had a very clear position on that, and he said: “a real watchmaker like you are, should not copy what others invented hundreds of years ago – you have to make your own developments”. It was a tough statement, but I took it seriously and refused that order, because it would have – I thought – turned the positive relationship with George Daniels against me, and of course I didn’t want that!
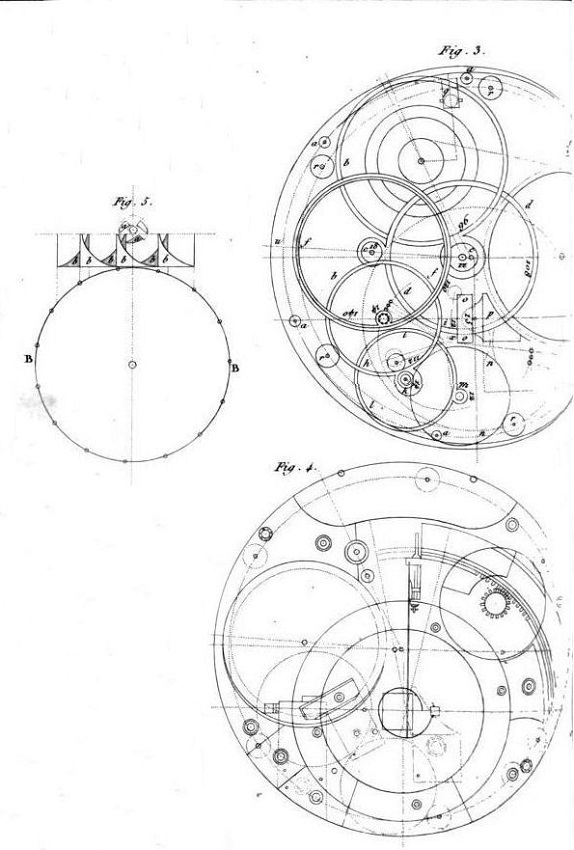
Plans for Harrison's H4 clock

Harrison H2 – photo, Wikipedia (user: Jonathan Cardy)
WA: When you were working in those days with private clients and auction houses, how do you think that helped shape your career as opposed to if you had worked at a particular brand, for example?
BL: If I would have gone to a big brand, I would have learned too early what watchmaking looks like in reality. Today, I am a watchmaker because of a big misunderstanding! This big misunderstanding was that for many years, I was convinced that to be a watchmaker, you have to master the making of each and every component. I was convinced that if I cannot make an enamel dial, a case, the hands, all kinds of screws – left or right turning, every pinion… if I cannot do each component, I’m not a real watchmaker.
Reality is quite different from that, but today I’m very happy with that misunderstanding of mine! I have been reading in books about the watchmakers of the past, about their skills, their specialization, hints and helps.
If I would have entered into a long-established watch brand, my knowledge would had been limited to their experience. I had the obligation, and by this the chance, to see what Arnold did, learnt about Frodsham, could see behind the curtain of Breguet, studied Harrison. I escaped the mono-brand limitation.
WA: So, would you say that influenced your personal philosophies on watchmaking? When you started learning about everything, what were your biggest influences and what did you enjoy the most of those different things?
BL: There was not much influence from only one special thing per se, but I am influenced by my little illness, and that illness is called curiosity! I am extremely curious. I want to know as much as possible. I always continued to ask the big question – ‘why’. My teachers started to hate this question because I always wanted an explanation.
That curiosity is what influenced me most, and curiosity also means that you’re not interested in well known or common things, but you always search for the unknown. I once realised that people started to talk about me, as ‘the last chance watchmaker’, when all watchmakers gave up, there was still me. I was convinced that whatever watchmakers had been able to make 300 years ago, 200 years ago, 100 years ago, we should be able to make as well.
WA: So, this curiosity and this want for a fundamental understanding of everything that you can, enables you to better innovate, and come up with solutions.
BL: Yes, and when you’re only in watchmaking, there might be a risk to be a little bit limited to solutions that are known in watchmaking. But being interested in old cars, in engines, in physics in airplanes etc, and even better when you know how to repair them, you can get your hands dirty, and that opens your horizons a little bit and I think this is very important.
WA: In 2000, you launched BLU – the Bernhard Lederer Universe – and the watches you made then were a completely different design language, with features like rotating dials and unconventional hand designs. Can you tell me about the process behind creating the BLU timepieces, and what drove you to create BLU?
BL: At first, BLU was meant to be Bernhard Lederer Uhrmacher, meaning ‘watchmaker’ in German. But we found out that for most of our customers it wasn’t possible to pronounce this word, so we decided to change it to Universe. When I started to build clocks I was influenced by my museum apprenticeship and all my clocks had been made in quite a classic way, and there was a moment when I realised that people will look at my clocks and think ‘we have to search for this watchmaker in the 1820 or 1830’, and they will not find me in those books where all watchmakers are listed.
I wanted to become a watchmaker of the 21st Century, not a watchmaker with a style of the past. Therefore, I started to make my first grandfather clock, a very modern sculpture with three pillars, and that was simply a design objective. I liked this and decided to make and design watches to express time differently.
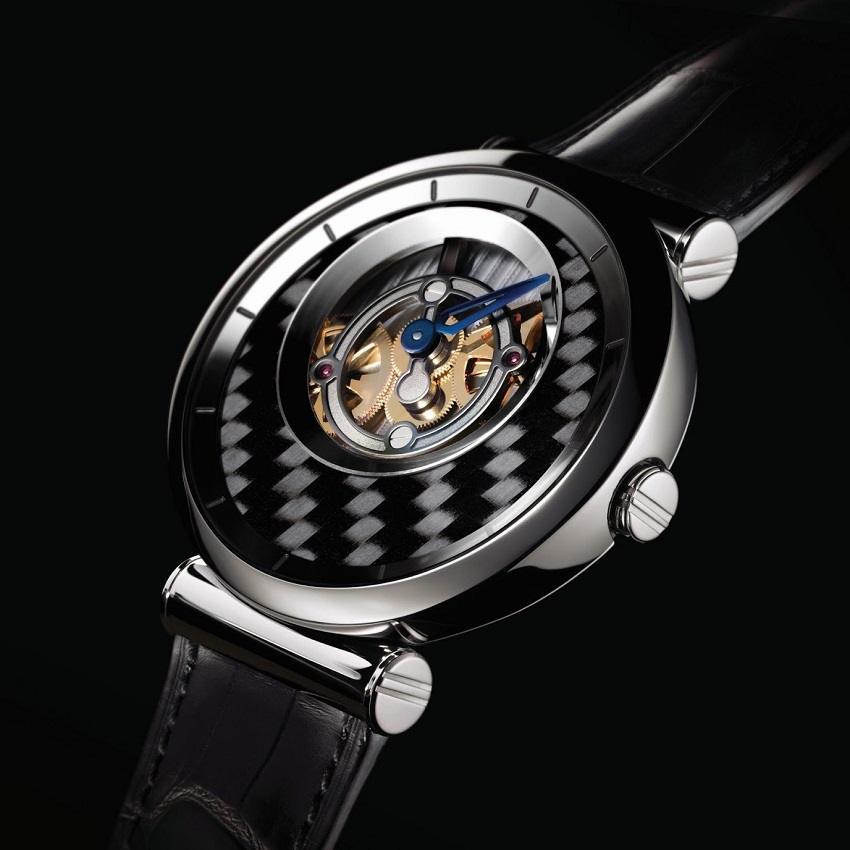
Bernhard Lederer Universe (BLU) Open Planet
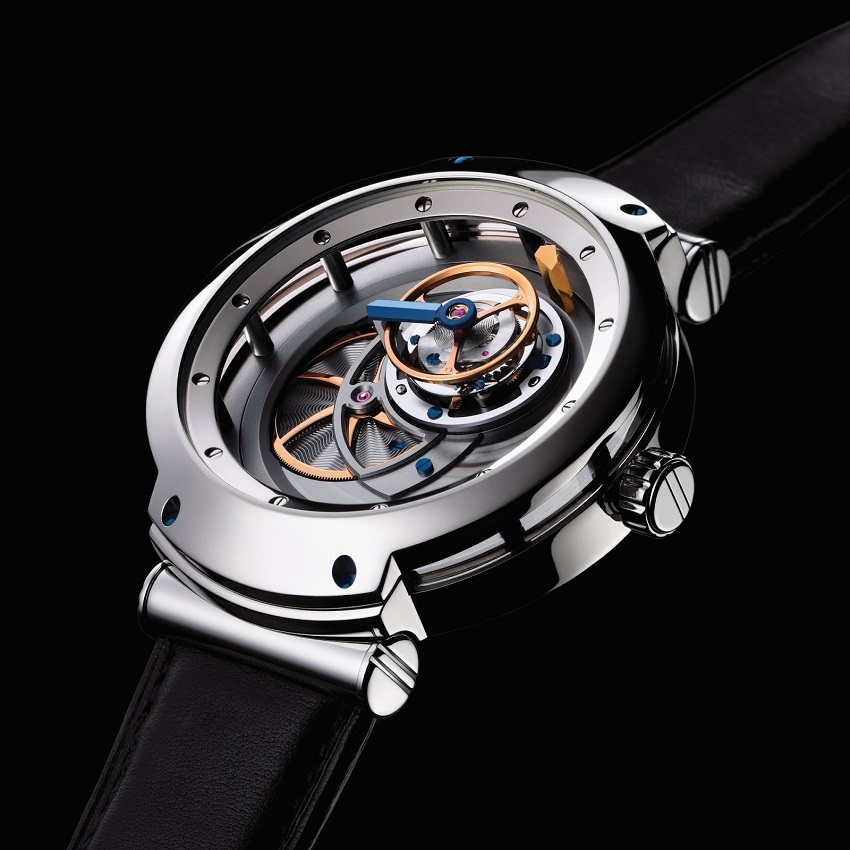
Bernhard Lederer Universe (BLU) Majesty Tourbillon MT3
When I was a little boy and had to start reading time, I felt this as something quite difficult. I always wanted to get a feeling for the time, but those two hands running around the centre of the dial couldn’t bring me this emotional contact. For a long time I mixed up the minute and hour hands.
So, the watch which today we call the Blue Planet, was working on an idea to have a watch where you can feel time. If you turn the hands, the whole dial turns and comes up to noon – then you’re on top of the day. Then it goes down, to the afternoon and evening. You don’t have to discuss the hour, you feel it. The only hand you can see is for the minutes.
Also, the Blu-Galaxy, which was based on a design from a German designer living in Brazil. He designed a watch with a retrograde fading out colour in a rotative way. I saw his designs published in a journal, and I thought he made a mistake – when he made it with discs, the lowest disc was the biggest disc as it has to be, so he showed the hours outside, then the minutes, then the centre seconds.
This indication is opposite to what we all had to learn: outside with the long hands are the minutes. I decided I would never buy that watch… even though I liked it!
So I decided to help this designer and called him in Rio de Janeiro. Eventually, we met in Germany, and I finally made the movement for his design watch. One thing came together, and that was a nice time.
And then came the time for a very special tourbillon, the Majesty Tourbillon, a construction which is extremely difficult to make as it is a tourbillon without a cage. The problem with a tourbillon, as Breguet had already realised at his time, is the weight of the cage. That is the reason why the flying tourbillon was invented, as you can reduce with this construction the weight significantly.
The teachers in the watchmaker school in Glashütte also invented the tourbillon that does not need any cage, only a base platform. They fitted the hairspring under the balance, doing this, means you have all the components on one side, and the only thing missing was the upper stone for the balance. They kept this with a bridge by itself as it doesn’t move, and the balance staff with the hairspring down under is turning forced by the hairspring’s placement on the lower plate carrying the other components – the escape wheel and the anchor.
WA: It was after BLU when you started MHM – Manufacture de Haute Horlogerie et Micromécanique. This is a different kind of operation, focusing on development of movements and complications, as well as restoration. It occurred to me that MHM seems more in line with what you have done previously in your career. I wondered whether this was something that you wanted to start before you created the Lederer brand? Was it a conscious decision to do MHM as a foundation?
BL: The story began in 2009. My wife was pregnant with our first daughter. This was when I was approached by an international operating structure asking me to develop several movements for them. Short before becoming a father and in the middle of financial crisis, you do not hesitate too long to take such a chance.
Some nice and interesting developments we made, such as the Gagarin Tourbillon, a lovely piece and a collectors’ item which came out of this collaboration.
When this contract came to its end, I decided to stay in developments, and coincidentally we received some orders directly when we started MHM – it continued like that and MHM became bigger and bigger.
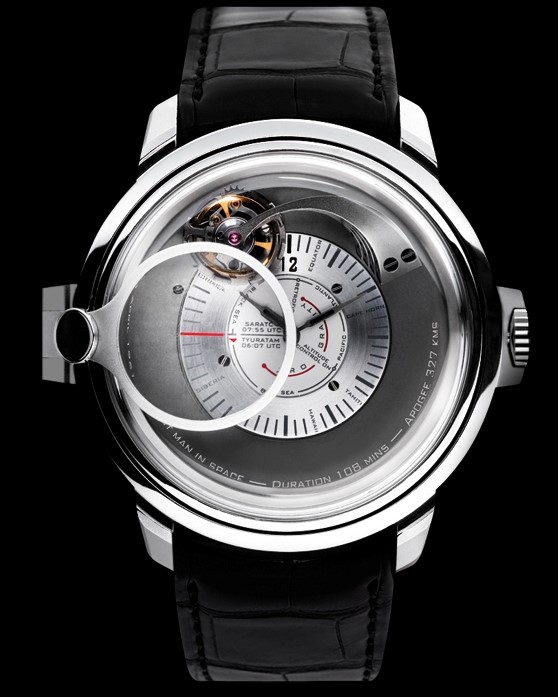
Gagarin Tourbillon by Bernhard Lederer
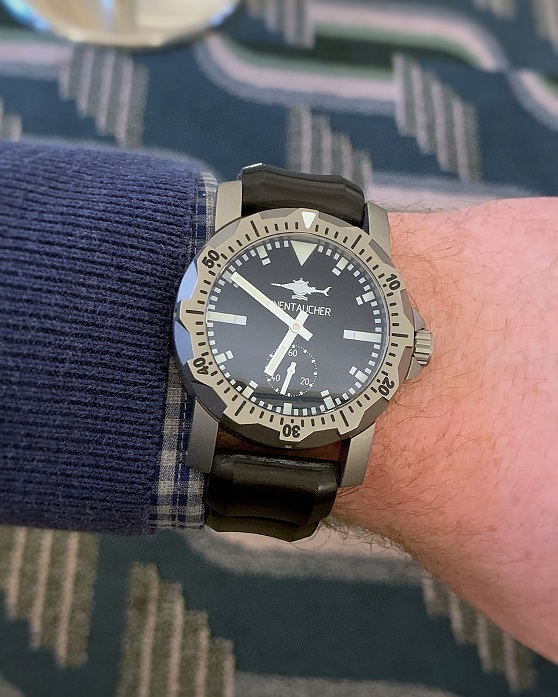
Antimagnetic dive watch by Bernhard Lederer / MHM for the German Navy
We made a fantastic watch for the German Navy, a completely a-magnetic watch that you can expose to whatever magnetic field, and it will never pick up any magnetism. It stays neutral and cannot be detected by the sensors of sea mines. The sensors are very keen on all kinds of magnetism – a simple quartz watch would be enough to explode the mine, and divers don’t want that!
After 13 years of developing for third brands, it was time to bring to the market what had been in my soul for years, and no Swiss brands wanted to have – the escapements. The heartbeat. The reason for a watch being. I understand why they’re not interested in those kind of developments, because the Swiss lever is so well experienced, so reliable, good for COSC certification, so there is no need for them to think about others.
When George Daniels convinced Omega to introduce the co-axial escapement, everybody thought about a new era and looked at them. Today they are starting to come closer to Rolex because of the co-axial, but if you look at how many millions they dropped to make that development… it is clear that the advantage Omega has is so little, that from a financial perspective there is no reason for the Swiss watch industry to create another escapement.
But for me, as a watchmaker who loves watchmaking and chronometry, there is no other field to be in. I am fascinated by being directly on the heartbeat and to refine the details in there.
WA: There is a lot of your work for Swiss brands that you can’t talk about because of confidentiality. But is there a question in particular that you really wish that you could answer?
BL: It’s a very interesting question, and I’ve never thought about it! And now as you ask me, I guess … no. I don’t want to talk about the developments that I made for others, because I made it for them and it does not reflect me.
That is one of the reasons also why I decided to stop developing for third parties and make my own watches. I can make those watches until I am 100% satisfied.
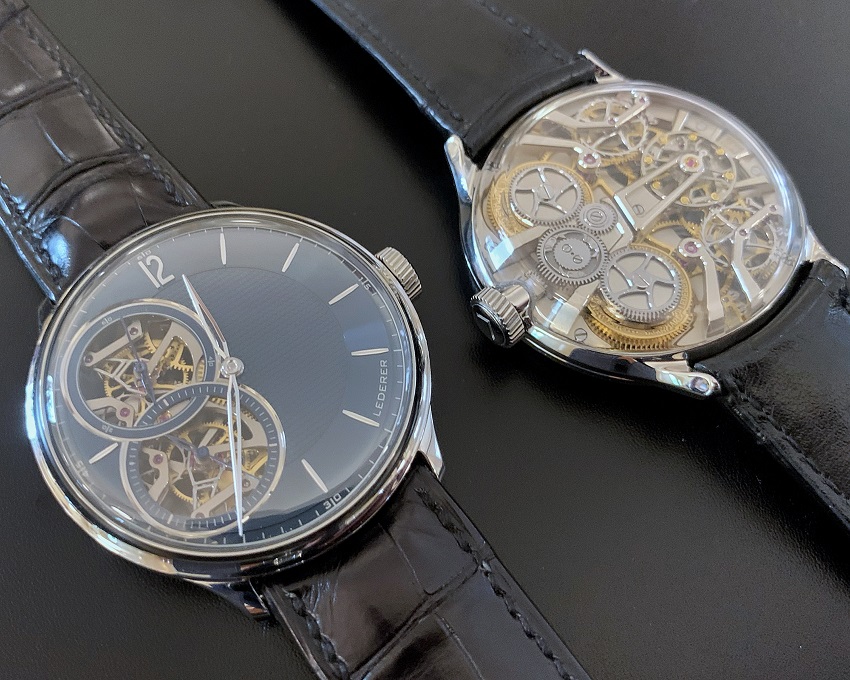
Lederer Central Impulse Chronometer
WA: You have set yourself a challenge to create a series of watches with different escapements in your Masters of Escapements series. The first of which was your Central Impulse Chronometer. Can you tell me about this project, and the challenges that you faced, and what did it mean to you personally to receive the GPHG Award for Innovation last year for this watch?
BL: In some ways, I am still a little boy. I looked at the notes of Daniels, and he noted that the independent double wheel escapement is too tight on tolerances to be put it into a wristwatch. That was the only explanation I could find in all the books, and so I did not reflect further. But he wrote that in the 1980s, after he had made the Space Traveller, and today is 40 years further on with more precise machines. At his time, he was working on more antique machines, so I understand why for him the tolerances had been too tight.
But what I did not take into consideration was that he probably did not realize from where the difficulty really came.
When you go to a wristwatch, you need to lift the frequency from 2Hz to 3Hz at least, and then you have a completely different dynamic situation in the escapement. Your balance works at much higher speed. That means you have to increase the power in the barrel houses to speed up the escape wheel much more, and you come into the problem of the law of acceleration. We could see on a high-speed camera, that this provokes a very strong moment of contact between the escape wheel and the impulse pallet.
The higher your amplitude, the later the wheel is reaching the impulse pallet. It goes so quickly between the two teeth of the escape wheel, that the impulse giving wheel really has to run full speed behind the impulse pallet and reach out at the very end to hit it. When you give more energy to the barrel houses, consequently it reaches to hit earlier. As you put in more energy, the hit is also much more aggressive, and when you see this on the camera, you start thinking about how long the teeth will survive.
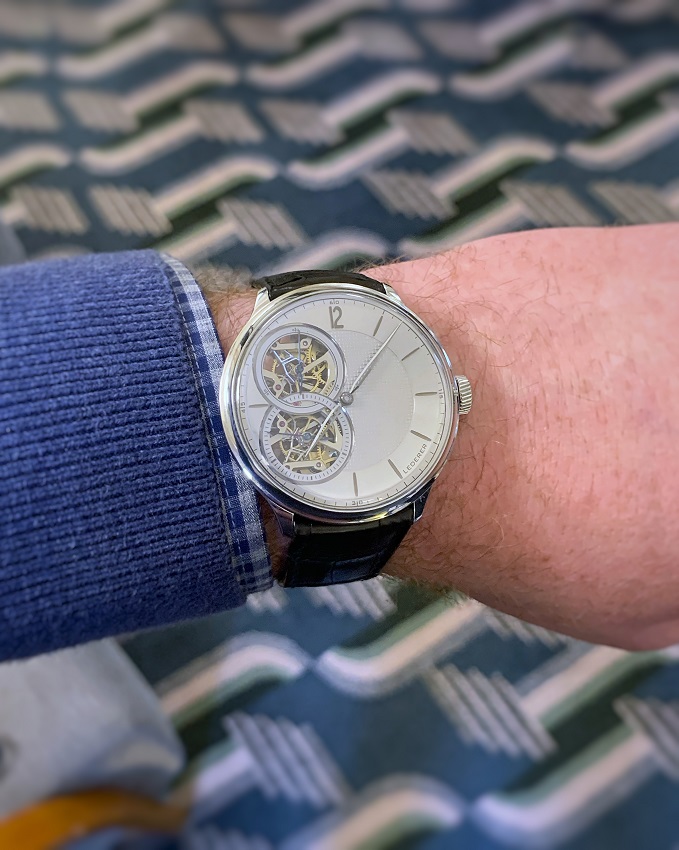
Bernhard Lederer's Central Impulse Chronometer
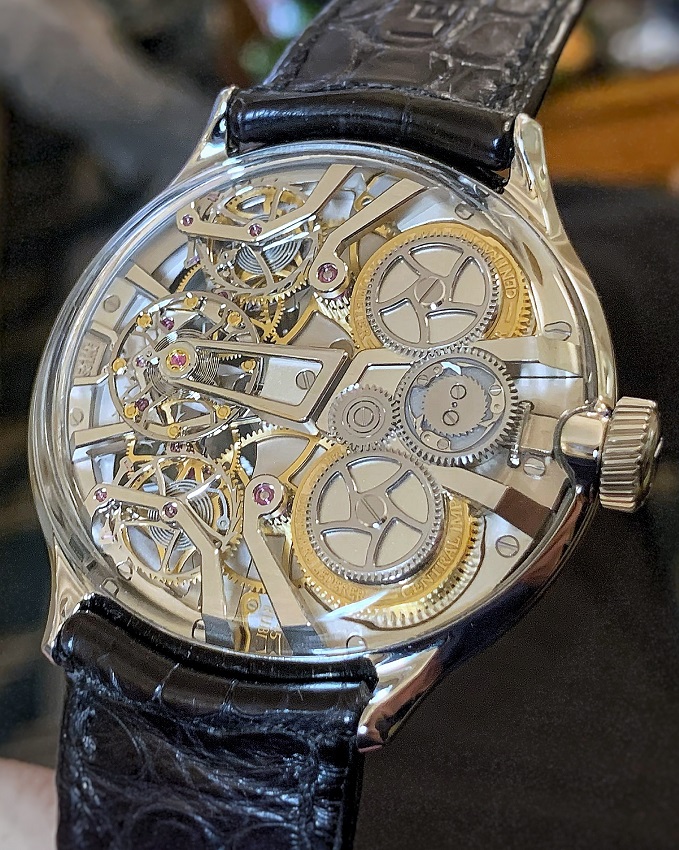
Bernhard Lederer's Central Impulse Chronometer caseback
I had to find a way to solve this problem. Finally, we invented something that is like a hybrid escapement specifically when we talk about low amplitude. When we have low amplitude, our escapement, the Central Impulse Chronometer escapement, turns into a hybrid escapement – a bit of a Swiss lever escapement and a chronometer escapement. From about 120 or 130 degrees on, it turns back and becomes again a pure chronometer escapement. In case of low amplitude, the Swiss lever escapement is there to ensure that not one single teeth can slip through and solidifies the whole construction.
By allowing a switch of the system from a direct impulse to a partial indirect impulse, even only a certain percentage, that helps ensure the energy in the escape wheel is always used. When I made George Daniels’ escapement a bit smaller and put it to 3 Hz, the difficulty is that you have energy in your escape wheel and if you don’t give it to the balance, you still have it, and you have to destroy that energy.
Compare this maybe to when you have a fan with three leaves – and you put in a pencil. The pencil will be pushed to the side, you let the leaf from the fan pass by and you put the pencil in again, it will always be pushed and pushed in a gentle and constant way. But if you don’t put the pencil in, let one leaf or two pass by, and only then put the pencil back, then you feel an enormous difference in forces and can imagine what will happen between escape wheel and the pallet in the detent.
If you keep the energy in the wheel and don’t transmit it to the balance, you have to destroy it on the resting pallet. Using the energy like this means you ultimately destroy one of your components. It’s a bit difficult for me to explain in English!!
Take a look at this slow-motion video showing how the Central Impulse Chronometer works
WA: You did a very good job – thank you! Staying with movements, I read a quote from you that said “Mechanisms and aesthetics are very closely linked. In fact, I would say they are totally inseparable in my watches”. I thought it was very true with the Central Impulse Chronometer on the caseback where with your mechanism, and the aesthetics of it, are front and centre. I was just curious to get your view why this link between mechanisms and the aesthetics of it is such an important part?
BL: Giving aesthetics to machines, to furniture, to objects in your surroundings, is a sign of respect to those objects. The aesthetics of a movement is the mirror of the values of the watchmaker. If you go to the past, just as I was today in Greenwich, look at the clocks there – the Harrison H1, H2, H3 and H4, every piece is made with love, with respect to what it should be because it should be part of a piece showing the most precious thing in our lives – the counting down of our own lifetime.
Watchmakers give all their love to design those objects to be beautiful, and this is a base respect that I feel deep in me.
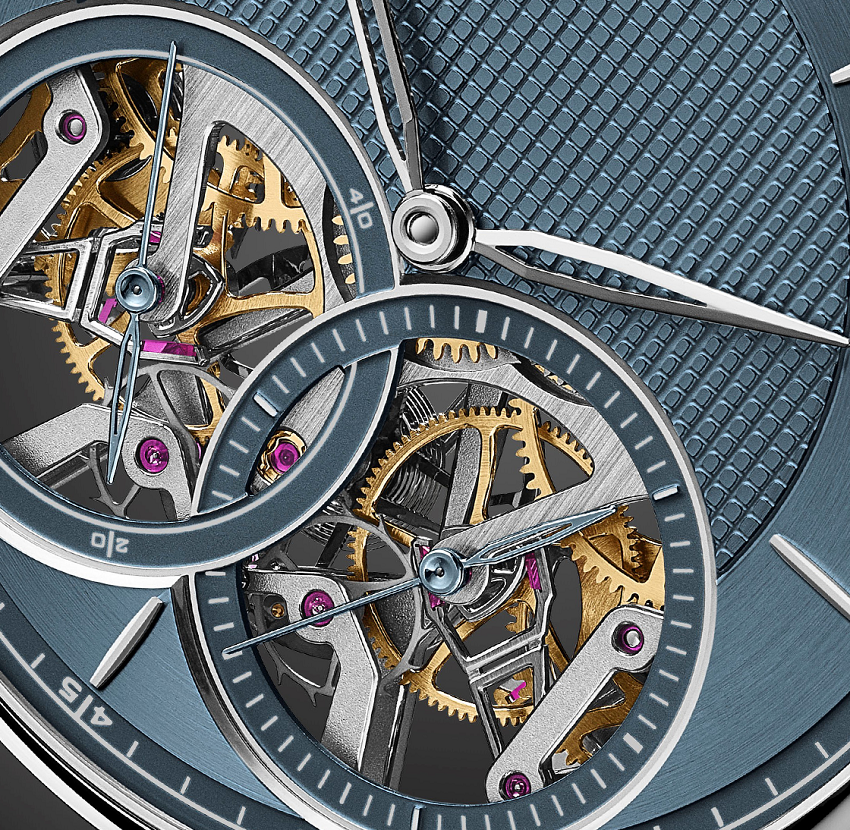
Central Impulse Chronometer dial – photo, Lederer Watches
As I told you, I love symmetry, I love form-follows-function, I love the natural beauty. When I made the Central Impulse Chronometer, at the beginning it looked completely different. The first one was almost in a Glashütte style with the chatons, with the three screws around them. Again, I made the decision that that’s not me, that is Glashütte, that is the past.
Also the case reflects this way of thinking: in the end, we made a case that is simply only for showing – a show case for the movement.
We started from the back to show I’m a watchmaker, I’m in love with this profession, with respect for all those inventors, whether that is Harrison, Le Roy, Arnold, Breguet, Dr Hook… when we designed that case, then I started to feel comfortable.
WA: Finally, if you could share one piece of advice from your career with an aspiring young watchmaker, what would you say?
BL: Stay with your vision. Follow your vision. I was asked at the Festival of Time in Waterford, in Ireland, a young watchmaker asked if he should go to a repair shop or to the school. I advised him to go to the school, as long as the school is implanted in a surrounding where other professions are also taught. When you go to watchmaker school, be careful to look for goldsmith schools, car repairs, plumbers, all different kinds of professions where you can drop in, discuss with those learning those professions. Stay curious and learn all around – not only watchmaking.
I guess it would be good to avoid repair stores because the owner of the store might tell customers ‘yes we could make it, but your watch is not worthwhile’, or ‘it costs too much’, or ‘it’s not possible to make today’. All is not true – everything can be made. Teachers have to look to the course, their salary is guaranteed no matter how many watches are repaired or not, but there you can really learn how to make every component of your watch.
Then you only have one difficulty. You have to find a job and learn a second time, because you only learned how to do it, you never learned that you have to do it quickly. That is then the second lesson – if you are not afraid for that second lesson, then go to the school.
WA: That has been fantastic, danke schön!
BL: Thank you!
To learn more about Bernhard Lederer, please visit LedererWatches.com, the MHM website, or our partners at The Limited Edition.
Be sure to also visit the AHCI website at AHCI.ch.
Remember to mention “Watch Affinity” when speaking with the team at The Limited Edition to receive a small gift with any Bernhard Lederer order!
Share your thoughts with us via our Contact page, or via our Instagram
Don’t forget to check out the Interviews Page for more!
You might also be interested in:
- Independent Watchmaking – An Ode to the Indies
- “It’s complicated”: the Co-Axial escapement
- Recommended Reading: ‘The Independent Spirit: Time makers since 1985’ by AHCI
- Watch Stationery and Gift Ideas
- Watch Books, Watch Boxes and more at the Watch Affinity Shop on Amazon (commissions earned)
As an Amazon Associate, I earn from qualifying purchases – thank you for your support
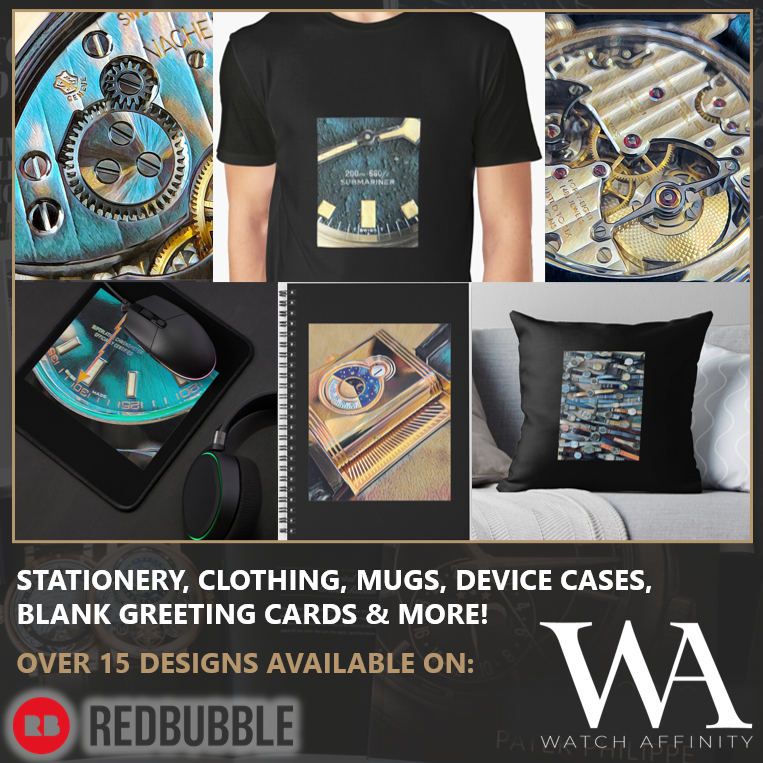
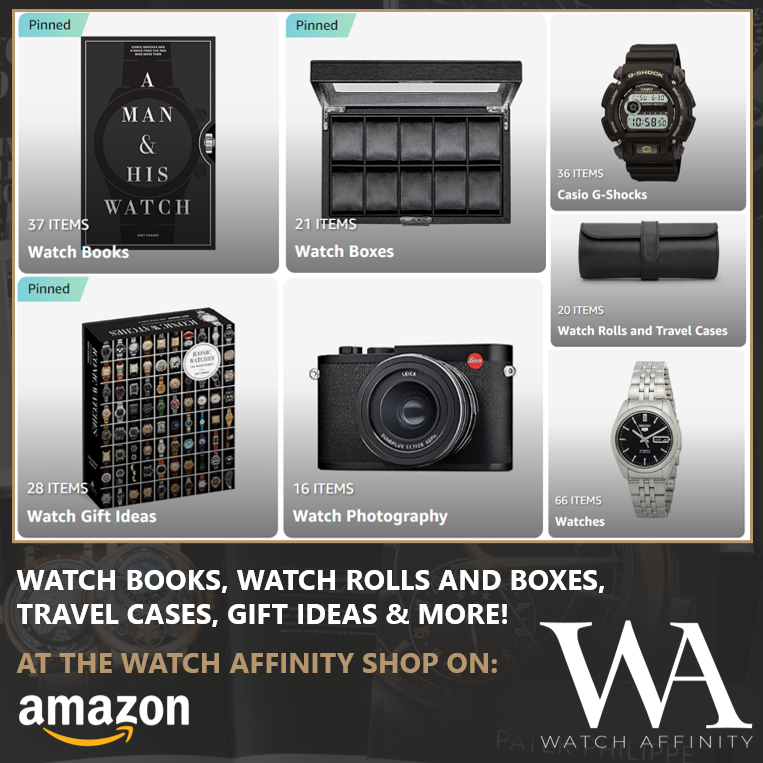