The first time I discovered Dr. Rebecca Struthers and her husband Craig Struthers work was, like with so many discoveries, via Instagram. The posts on the @StruthersWatchmakers account often feature photos and videos from behind-the-scenes, highlighting the handiwork that goes into the making of their own watches, as well as restoration of historic pieces, which is at the heart of what they do, and all the while using traditional techniques.
Ahead of the publication in April this year of her first book, Hands of Time, I sat down with Rebecca Struthers to learn more about her career to date from studying jewellery to becoming the first British watchmaker to earn a PhD in horology!
In Conversation with Dr. Rebecca Struthers
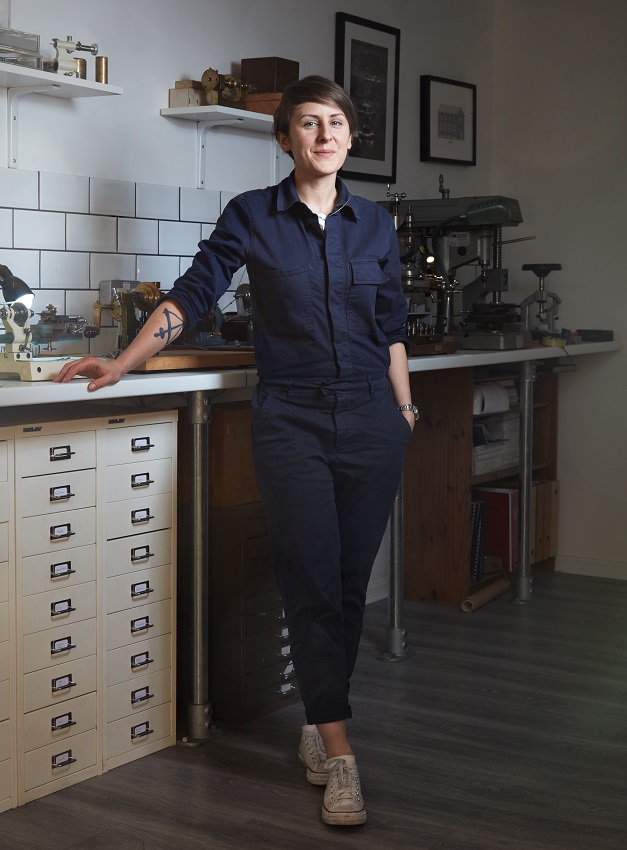
Dr. Rebecca Struthers, photo – ©Andy Pilsbury
WA: To start with, can you tell me a bit about your journey – you started out training in jewellery, and ended up with your own restoration workshop, becoming the first British watchmaker in history to earn a PhD – it is quite the story!
RS: I always think I have the boring story and Craig has the interesting one, as he did other things first, whereas this has literally been my life. I went to a very academic school that really pushed science, but I’ve always had this combined love of art and science. I struggled with school and dropped out half-way through my A-Levels to go to art school. I grew up not far from the School of Jewellery in Birmingham, so I knew about it being from the local area.
The course looked interesting, I loved the space, the building, and so from the moment I visited I knew I wanted to give it a go, and so I went and did two years of jewellery and silversmithing. At that point, I didn’t really realise that watchmaking was a career. I’m not one of these watchmakers who always wanted to do it from childhood and played with my grandparents’ watches, I discovered it whilst studying jewellery and silversmithing, and found it by accident.
It happened to be taught at the same university that I was at, and a few watchmakers saw my work where I was introducing movements to jewellery, and they asked if I had thought about studying watchmaking. They invited me to the workshop and I had a look around and it was like an epiphany moment for me – you get to be an engineer and scientist, but also an artist and designer at the same time, and a historian too – all my favourite subjects under one roof!
WA: I know what you mean, I don’t think there is anything else where you can get a combination of all those things together and it makes watchmaking really unique!
RS: Definitely. I love how varied every day is, everyday it’s a different project, a different challenge, it constantly keeps me entertained. You’ll never learn everything!
I’ve always loved the atmosphere of workshops ever since I first set foot in one, even my grandad’s garage as a kid with hammers, saws, massive vices strapped to huge wooden benches, the smell of oil and dust. That was it for me – I’m just one of those people, I think!
I like working with my hands and I like studying. With my doing the PhD as well, I was at university for 13 years in total doing one subject or another, but also working full time. By the time I got the PhD at 30, I also had 14 years in the industry including working at the retail end and starting jewellery at 17.
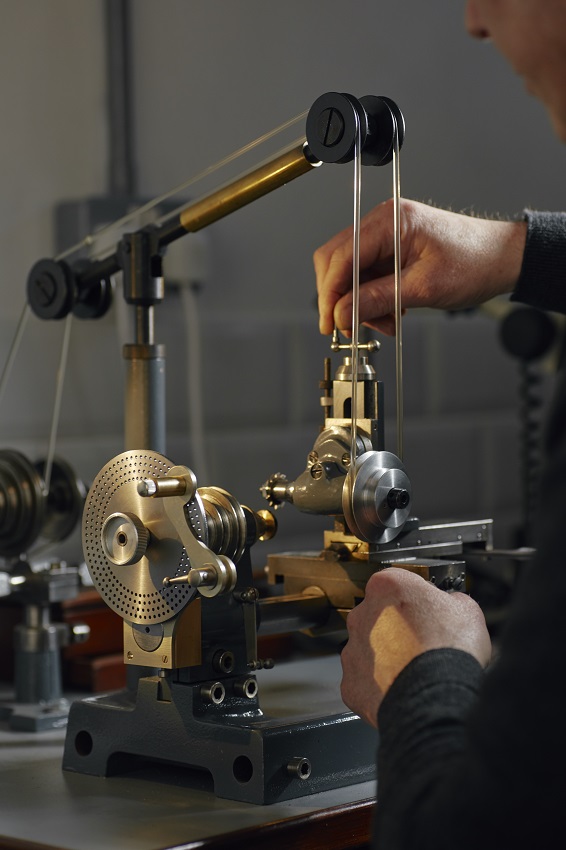
Inside the Struthers workshop, photo – ©Andy Pilsbury
WA: Were there any skills in particular from working with jewellery that transferred well into watchmaking?
RS: Hand skills, for sure. I was really lucky because the course that I did in jewellery and silversmithing was axed the year after I graduated from it and was really practical. My tutor had been in the profession since he was 13 and retired the same year as the course closed. He was a master goldsmith with a huge amount of knowledge. It’s hard to learn those practical skills now, a lot has moved to being more academic, lots of writing, research, but if you can use files and piercing saws, and you know how to make with your hands, those are transferrable skills in whatever you’re doing.
Things like case repair as well are very much part of jewellery and silversmithing so that means I could go straight into doing quite a lot of work on cases, and I still use the skills I learned doing jewellery now with our watchmaking.
WA: Was it a difficult decision for you and your husband Craig to start the Struthers Watchmakers workshop in 2012? Were there aspects of this process that turned out to be easier or more difficult than you had anticipated?
RS: Everything was more of a challenge than we had anticipated!
We were living in London at the time, and I was really struggling with work. I’d had a few quite challenging job experiences; it’s not always been the most welcoming industry for women. It’s been 20 years since I started out, and I’ve seen a lot of change in those 20 years but initially it was a real struggle, and I was feeling like I wasn’t going to fit in anywhere.
Craig was supporting me, and I said that I’ve got to do something completely different or retrain, because I can’t keep going in this. He didn’t want to see me like that; he had been self-employed for a while in the past, and he suggested just doing our own thing. It was either that or give up – I wanted to stick at this, there’s nothing about the subject that I’m not madly in love with, it was just the politics.
We decided to give it a go. We had a small business loan, and no other financial back-up, and in retrospect we were incredibly naïve! The process was a real uphill struggle, and the first few years were touch and go. It’s taken the best part of 10 years to get the point where we’re comfortable, and now we’ve got work booked in until 2028.
I think it’s quite easy to start with a bit of a bang. People are interested in a story they haven’t heard before, so when we first started out advertising making our Tailor-Made watches – making the cases, completely refurbished heritage movements that we salvaged and rebuilt them from scratch, making our hands, case, the dial, everything – when we started advertising, we got a load of press, got an order or two, and thought we were up and running. Then the press fizzles out because it’s not a new story anymore, those orders have gone out, and then it’s tumbleweed.
You kind of think this will just keep going, you don’t anticipate that you need to do anything else, but that’s when the slog begins.
Also, pricing your work is a really hard thing to learn, and I think that’s a universal thing for craftspeople as well. Every maker I speak to is terrible at charging properly for their time. We’re our own worst publicists!
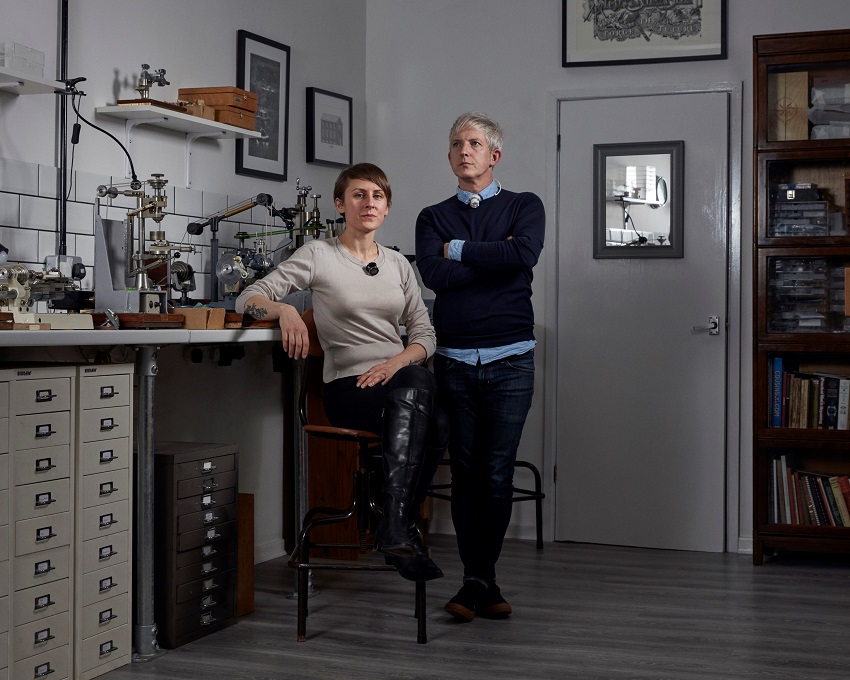
Dr. Rebecca Struthers and Craig Struthers, photo – ©Andy Pilsbury
WA: I found Struthers on Instagram, I particularly enjoyed the photos and videos of the behind-the-scenes making process. I like seeing the work, the craft and the detail, and everything that goes into it. That was maybe a different approach to publicity, and I loved it!
RS: Craig worked really hard on the videos. You don’t see enough making – lots of people talk about making watches, and not many people show it, especially traditional watchmaking and hand-making. I read a while ago one of the big brands in Switzerland saying no-one wants to see dirty hands and a watchmaker hunched over a bench anymore, they want to see the lifestyle. That just isn’t us – we like the oily hands, and the reality of it I suppose. We love sharing what we do – it’s not about having a big audience or anything, it’s just about showing that we’re making and sharing what we enjoy.
WA: I think it’s important to see what goes into making watches, without that I don’t think you can fully appreciate what it is that you’re holding, or what’s on your wrist. I especially like that you have a strong focus on traditional methods and tools, with a lot of your work being restoration and custom projects for clients. Can you tell me about some of the most interesting, challenging and rewarding projects you have worked on?
RS: Some of the watches we work on we can’t talk about, so I can’t go into too many details. This is going to sound weird, but I love cleaning things like rust! There’s something immensely satisfying about taking a ball of rust that looks like it has come off the Titanic, and turning it back into a functioning watch again. Those are some of the biggest projects we’ve worked on, some of them can take years because you have to soak parts apart and try to save as much as you can, so they’re really challenging, but I love those kinds of projects.
Making-wise, 248! Making our own in-house movement has been an incredible challenge. We had this vision that it’d be done years ago, but it’s taken a lot longer and we faced more challenges than we thought we would, but it’s been a phenomenal learning curve. We see it as our school watch! Now we have the blueprint, we’ll be making one a year for the next 10 years, and that’s it.
That’s probably our biggest challenge to date, but again I love it. I like constantly pushing myself to do new things, and that’s a big part of what we do. I think if you’re ever at that point where you think this is as good as what I’m making is going to get, then I think it’s probably time to call it a day.
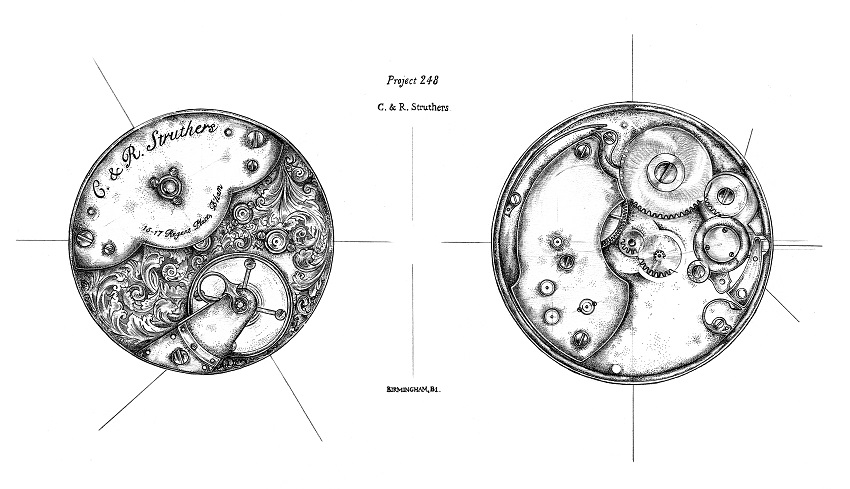
248 Illustration – Struthers Watchmakers
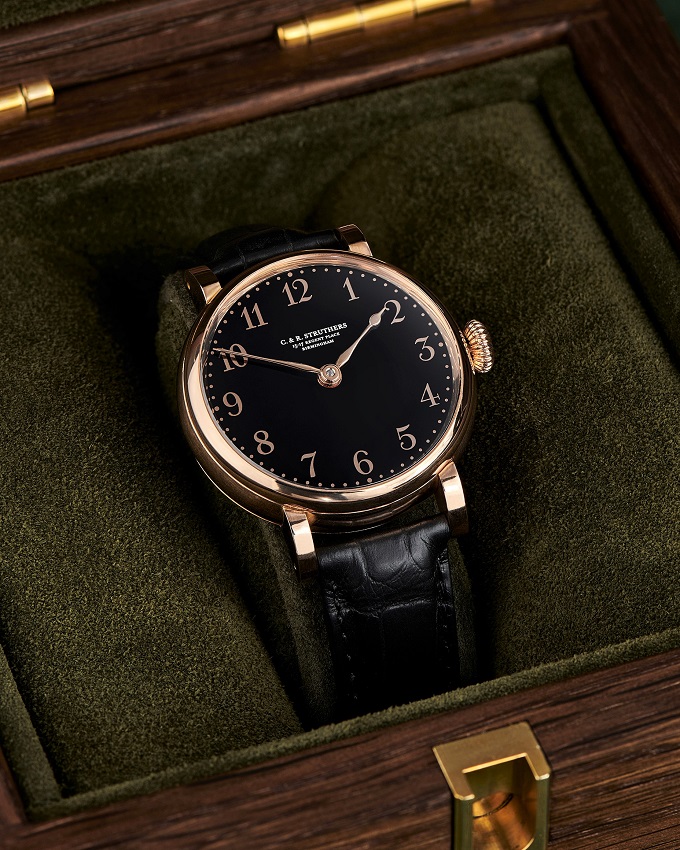
Struthers Watchmakers 248, photos – Struthers Watchmakers
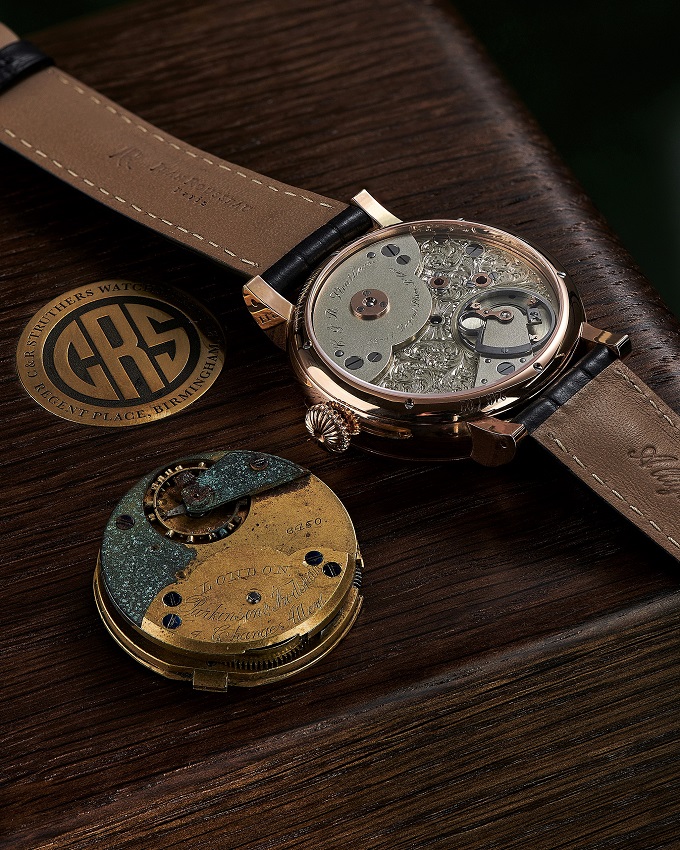
WA: On a personal level, what does it mean to you to have created your own movement, and having your names on the dial?
RS: I think it’s really special. When it’s your name on the dial it’s something you’ve made, we don’t have any staff, we don’t have apprentices, it’s literally “C&R Struthers” because C&R Struthers have made all that’s in front of you now. That was important for us with 248, and we separated it from Tailor-Made as well which is signed Struthers.
Coming from a restoration background, working on hundreds of years old watches, you see these makers’ names that are engraved in metal, who passed away hundreds of years ago. We know that making these watches now, if they’re looked after, in hundreds of years’ time there will be something around that we’ve made with our name on it. It’s like a legacy in a way, or like a mechanical ghost that I’ll leave behind on this Earth when I’m gone!
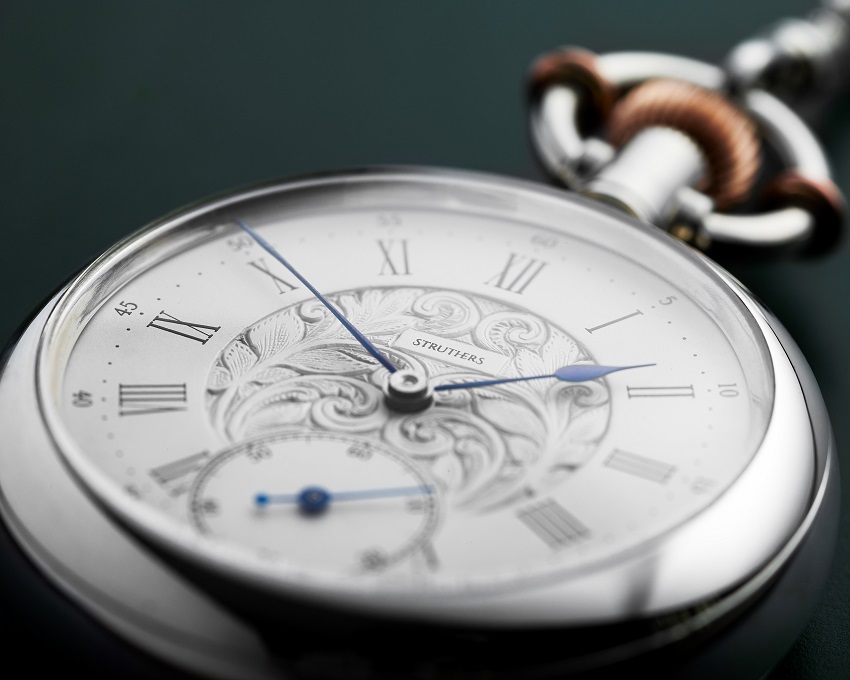
Struthers Watchmakers, The Carter, photos – Struthers Watchmakers
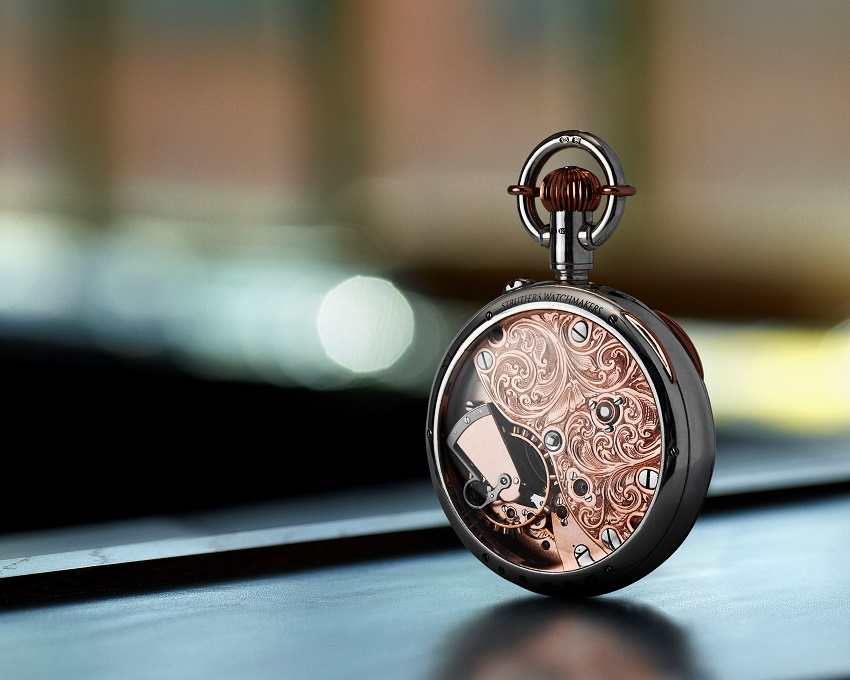
WA: In 2017, you became the first British watchmaker to earn a PhD in horology. Can you tell me about how you went about this?
RS: Non-practitioners have studied subjects that involved watchmaking, but no watchmaker had studied a PhD in watchmaking. It really excited me at first, the idea of being the first watchmaker to do this, and when I finished, I realised I’d qualified myself for a job that didn’t exist! It was a natural progression for me because restorers are, in part, historians, because you have to know how the movement was made to restore it.
I love writing and research, so balancing the two together was a natural and enjoyable thing. Being in watchmaking 24/7 also helps, because doing it all day every day there’s no having to get your head out of one space and into another, so you’re just constantly in the zone.
I did my Masters in History and Art & Design, and it was one of the tutors who had read my Masters dissertation who suggested it. Just as I never thought about doing watchmaking, I’d never thought about doing a PhD – I was the first person in my direct family to go to university, so it wasn’t on my radar. It sounded fun, so I went for funding through the Arts and Humanities Research Council to afford it… and got it!
It seemed a natural way to research, this is why I’m amazed that there aren’t more practicing watchmakers who do something like this, because you can bring something completely new to the table. If you’re a historian researching clocks, or watches, or any three-dimensional object, all you can see is the outside and you’re limited by that. Anything to do with the technical details about how it was made, any clues about how it’s worn or been repaired, you must either outsource that or accept that fact that you’ll never really know.
Whereas as a practitioner, you’ve got a full three-dimensional, 360 degree, internal and external view of everything, and that was the cornerstone of my PhD. I spent a year in the basement of the British Museum pestering curators and taking apart 30 watches in their collection, some of which went through forensic analysis too – we did XRF and x-ray scanning on them to look at how they were made and what that could tell us about their story.
What I found was a watch that basically had been called a Dutch Forgery, and completely dismissed from research because it was a bit cheap, tatty, and not very glorious in the history of horology. These watches were the first commercial fakes that were produced on any real scale. They started the journey in the reduction in value of the retail price of watches, to the point that they were accessible to all, so really this is the beginning of the democratisation of accessible time.
They were cheap and badly made, so they had been ignored, but I found this whole history behind them. Because they were forgeries, there was a lot of smuggling – tracking these watches back in time 250 years and across Europe, trying to find out who was making them, where, how and why they were getting to market, all through these hidden marks. I couldn’t have done this if I wasn’t a watchmaker.
WA: It’s interesting, obviously there is a lot of forgeries and fakes today, but you wouldn’t necessarily think of that as part of the story and history of horology, by default we focus on the authentic. But it is there, and you’re right that that story is a part of how things have been shaped to be ultimately where we are today.
RS: Fakes can be such damaging things – damaging for brands, collectors, and it’s easy to understand why they build up so much resentment that people want nothing to do with them. But they also tell us so much about our society and our cultural values at the time, they can tell us so much about the changing landscape of how things are made.
The places that these Dutch Forgeries were originating were around the Swiss French border – the same areas that grew to become the huge watchmaking centres that we have today. In many ways, the financing from these watches went into the industry as we know it, and it was the start of the shift between British watchmaking being the centre of world watchmaking, moving to Switzerland. They tell us a huge part of why we are where we are today, if we can get past the initial “ah, I hate them!”, they can tell us so much, so they’re worth studying, I think.
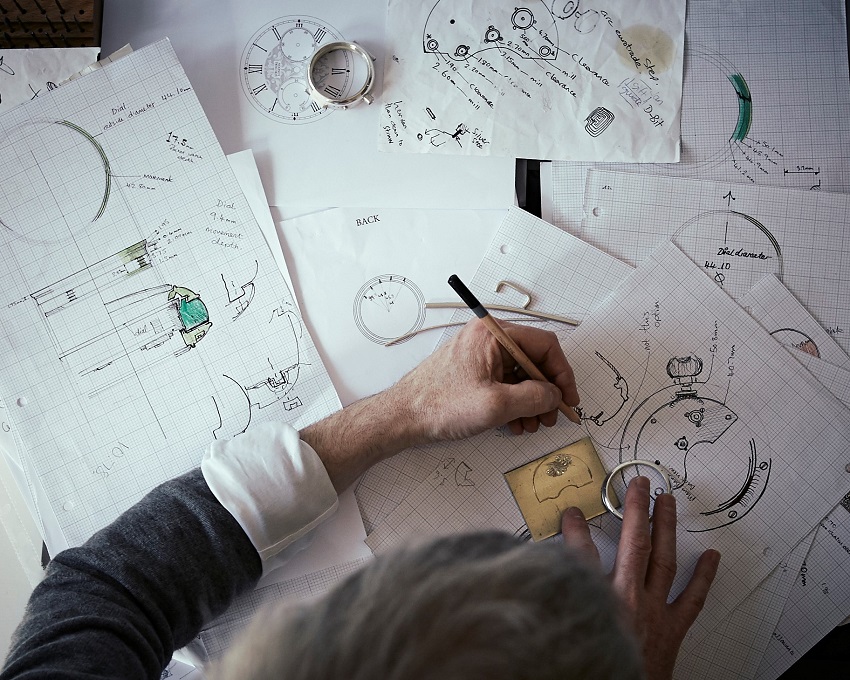
Struthers Watchmakers design work, photo – ©Andy Pilsbury
WA: Whilst I think there is an awful lot to be said for “learning on the job”, I think formal paths of education are equally integral in preserving the traditional skills you practice today for future generations of watchmakers. From your experience, what do you think are the best ways of ensuring these skills are never lost to the annals of time? What role would you like to play in passing these skills to the next generation of watchmakers?
RS: If we start looking now at the next generation, in the UK we’ve lost so much of our design and craft skills, even at primary school for kids learning how to do things with their hands. I remember taking stuff apart and making things from as young as I could hold a pen, a pair of scissors, or a screwdriver to start trashing my parents’ things! They were very patient with me which I’m grateful for, and it was part of my life from a very early age. I was encouraged to interact with things, make things.
There’s an important part of making that I think gets forgotten about: it’s the confidence to be bad at something, and that it’s OK to be bad at something and to take time to learn. Just like musical instruments – you have to be bad at it for a long time before you’re good. And that’s OK. It’s a cornerstone attitude that I think we’ve seen being lost and is flowing into craft skills. Young people come into this, they’re terrible at it, and they don’t want to do it anymore. But every master watchmaker was a terrible watchmaker at some point, you’ve got to plough through it.
It’s OK to fail, it’s OK to break things, because you’ve got to learn, and that’s the only way you’re going to learn. So seeing more of those skills be brought in at primary school level, through to secondary school level, encouraging kids to be doing things with their hands. Understanding that it’s going to take time to learn and get good at these skills, so by the time they get to college they’re already in the mindset of giving something a go with the view to being half decent at it in three to five years.
We have a very instant culture now; we expect to access things and be good at them straight away. And that’s just not how all heritage crafts that I can think of work.
Making is good for you, it’s good for your mental health. We also massively undervalue craft skills to a criminal extent in my opinion, they are beneficial for so many things in life. A cardiovascular surgeon Roger Kneebone went on record a few years ago saying he was having to send his first-year students for sewing lessons because they couldn’t do basic stitching. You wouldn’t think that learning to sew at school might help you learn to be a surgeon when you’ve got to sew someone up after operating on them! These skills have so many other applications.
WA: That certainly isn’t a link you would immediately make, for sure! Later this year sees the publication of your first book, ‘Hands of Time‘. Can you tell me a bit about what we can expect from the book?
RS: So, it’s 27th April for my UK edition, and 13th June in the US.
It’s a watchmaker’s history of time, told through the objects that we’ve invented to measure it with. I take you back 40,000 years in time to when humans first realised that time was a cyclic thing that could be measured, and then how we progressively broke time down into smaller and smaller parcels to help us doing everything, from planting food and agriculture, right the way up to atomic time and travelling into space.
It’s very much told from my position as a watchmaker, too, so I take you into the bench and through my hands, looking through my eyes at some of the amazing pieces I’ve worked on over the years. There’s lots of stories about watches too, lots of making techniques, and what I mentioned before about looking at watches to see how they were made and how they have worn as well from the repairs that they’ve had.
I wrote this to very much be the book for watch geeks to give to the significant others in their lives, to convince them that the thing they love is a fascinating and enjoyable subject. It’s for a broad audience, and kind of a “this is why I love what I do”. I’m calling it my ode to watchmaking, a watchmaker’s ode to watchmaking!
(Update: read my review of the book here)
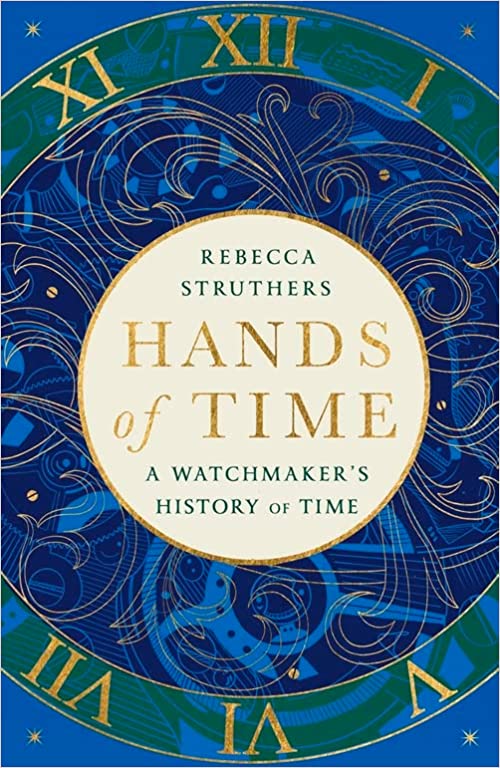
Hands of Time by Dr. Rebecca Struthers is published on 27th April 2023
WA: The way you described it, it sounds similar to what you said earlier with your PhD where you had the making side, but also a much broader history side, too. Would it be fair to describe the book as exploring how those two things relate as well?
RS: Definitely. It’s how I work when I’m at the bench making things, when I’m a researcher, and how this book works too. I can’t separate the subjects in what I do, they’re so infused with each other.
Even making 248, we looked back to a movement that was made about 150 years ago as our reference and worked from that. When you’re used to repairing things that are a few hundred years old, and you know that what you make now will be around in a few hundred years, having that knowledge of which designs worked and which didn’t age very well, this is easy to repair and make new parts for and this isn’t, it completely informs the way that we make watches now.
For me, how I judge whether or not a watch is good quality is probably different to most other people. A good quality watch is easy to service and restore, that’s my baseline and then you build from that. For me to feel comfortable saying this watch is six figures, I have to feel confident that it can be restored when I’m not around to look after it. When I see some of these modern watches, it’s a huge amount of money, and I don’t envy whoever is going to be in the service centre taking these in, even in 30-40 years. I want something I can have total confidence in the longevity of.
WA: How would you describe your own philosophies of watchmaking and horology?
RS: Ease of restoration, and the quality of the materials and craftmanship are important. That’s another thing which follows from studying jewellery from before, my tutor told me to only work in materials that are worthy of your work. When you think about the price difference you can charge between say a steel case watch, or a gold case watch for the same model, even for a mass production brand, the amount of work that goes into creating the two is virtually the same. Yet for a gold piece, you can charge more than the additional gold value, because of the perception of the value of gold versus steel.
If you’re going to hand-make something, and spend years doing it, why would you devalue your own work by making it in something that people will never perceive as having value? Match the value of the material to the value of the effort that you’re putting in. That’s why we only work in precious metals now, because if I’m going to be working on something for years of my life, that’s worth the investment in the material as well as the investment in my time.
WA: What’s next for Struthers Watchmakers?
RS: Surviving the next year with my book! I’ve got a very busy year with it ahead, going on tour and doing some events, and hoping to sell a few copies! This is what I’m trying to do in getting the subject out there, and hopefully introducing people to watchmaking through this book, and I’m hoping to do a children’s book version too, introducing the subject to kids from possibly three to five – to be confirmed!
We’ve also got the last 5 in-house movements going out at the moment, then starting the next ones of those. We’re doing a new version of the Kingsley, which is starting this summer, but they won’t be going out until 2024. Everything is years ahead, so what we’re doing now, you’ll see happening in two to three years.
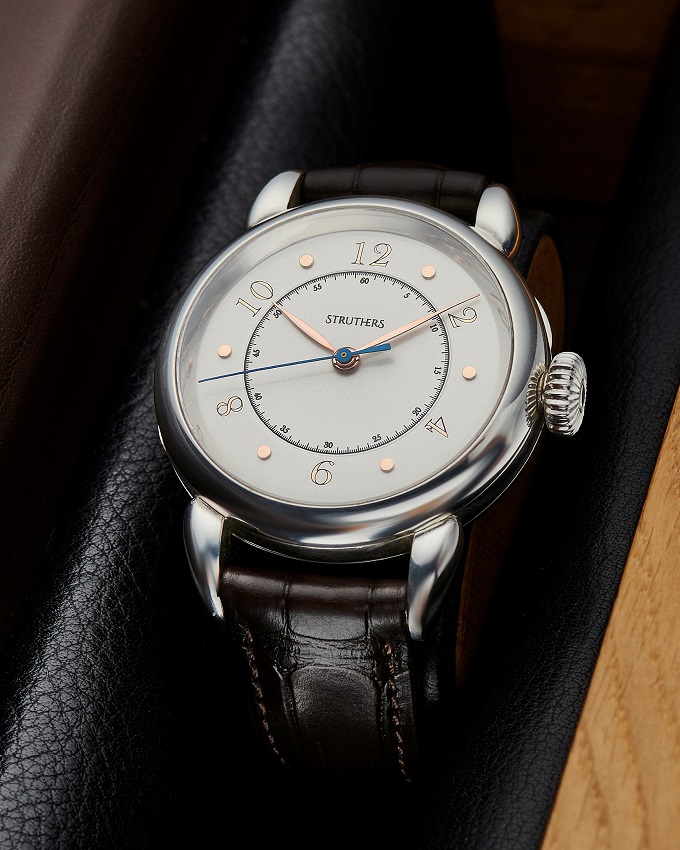
Struthers Watchmakers, The Kingsley, photos – Struthers Watchmakers
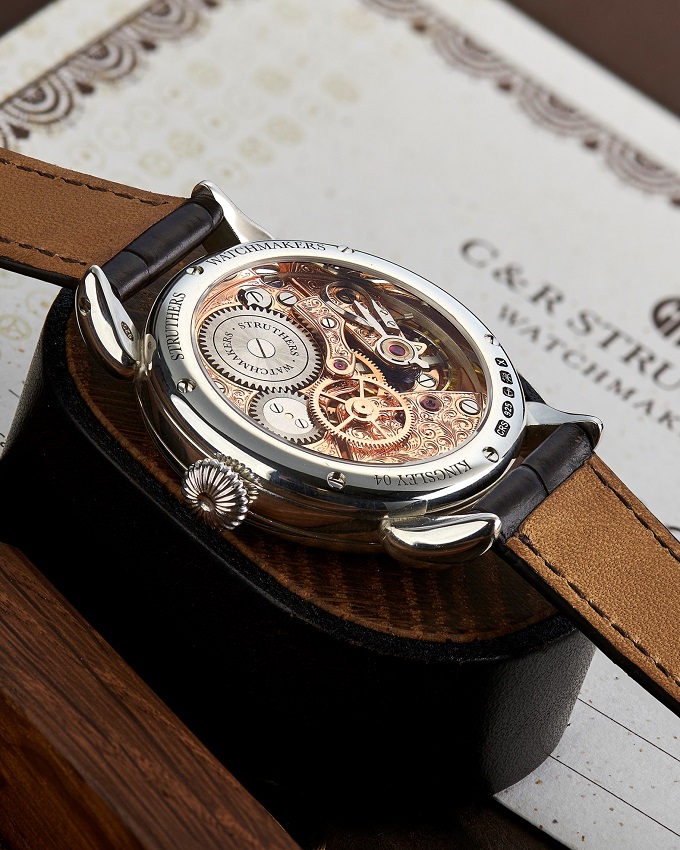
WA: Finally, if you could share one piece of advice you learned over your career with an aspiring young watchmaker, what would you say?
RS: It’s OK to not be good at something while you get good at it, and don’t be put off if things don’t work first time, or you’re not an overnight success, that’s normal.
We only hear stories about the people who have succeeded, we don’t tend to have a very honest backstory of the 20 years they failed before they succeeded, so don’t be too hard on yourself. Keep going. I wish I had someone on my shoulder saying, “it’s OK Rebecca, it’s supposed to be this hard, you’ll get there eventually!”
WA: Great advice! Thank you so much for taking the time to speak with me and best of luck for the book launch!
RS: Thank you very much!
Hands of Time is available here (commission earned)
To learn more about Dr. Rebecca Struthers and Struthers Watchmakers, please visit StruthersWatchmakers.co.uk or follow @StruthersWatchmakers, @Rebecca_Struthers, and @Craig_Struthers on Instagram.
Share your thoughts with us via our Contact page, or via our Instagram
Don’t forget to check out the Interviews Page for more!
You might also be interested in:
- Recommended Reading: ‘Hands of Time – A Watchmaker’s History of Time’ by Rebecca Struthers
- Watch Finishing Techniques
- Vintage and modern watches – the pros and cons
- Watch Stationery and Gift Ideas
- Watch Books, Watch Boxes and more at the Watch Affinity Shop on Amazon (commissions earned)
As an Amazon Associate, I earn from qualifying purchases – thank you for your support
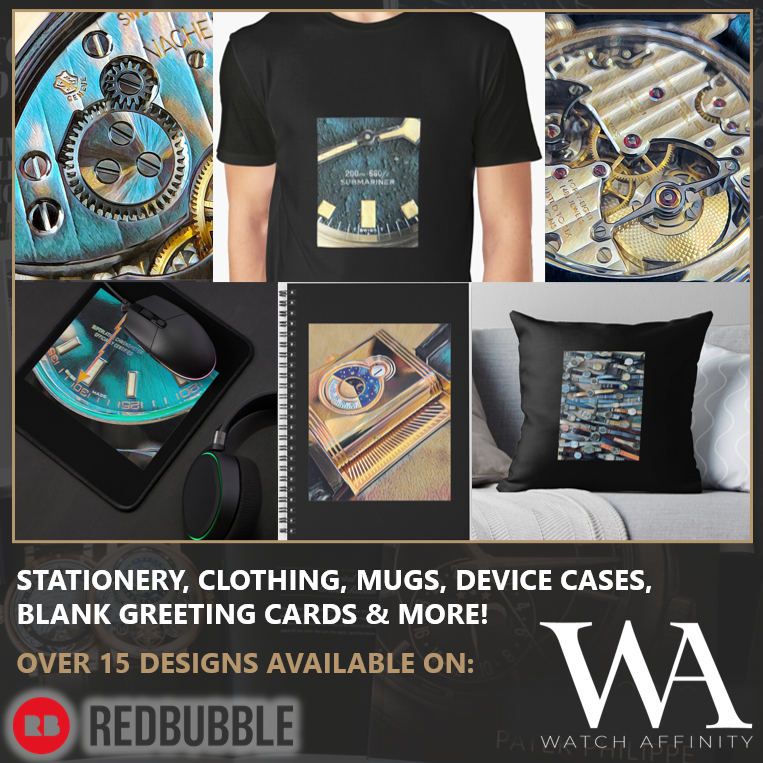
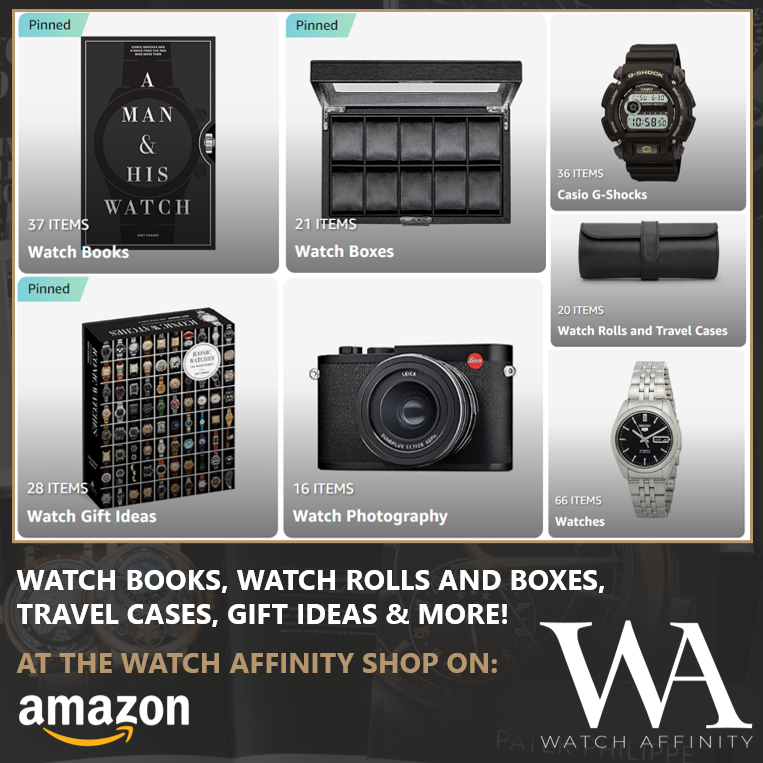